Construction de bateaux: Construction de base en résine, fibre de verre et Noyaux
Beaucoup de gens se demandent comment les bateaux en fibre de verre modernes sont construits, et la construction de bateaux aujourd’hui n’est pas du tout comme à l’époque de la construction de bateaux à moteur anciens et classiques. De nos jours, la construction de bateaux est en fait assez high-tech.
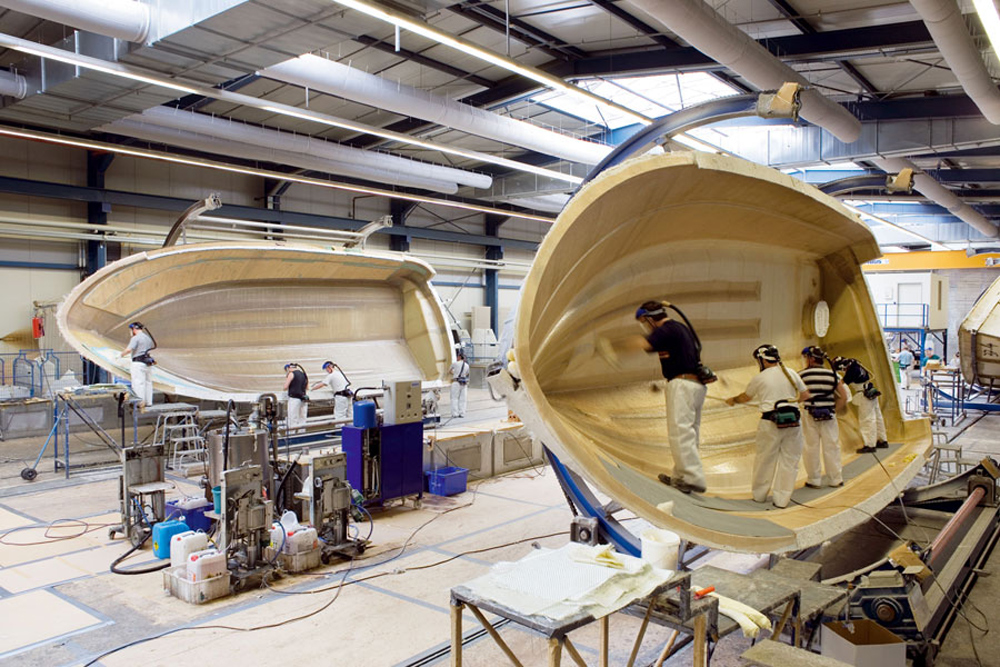
À l’ère moderne, la construction d’un bateau commence par un moule. Ceux-ci seront utilisés pour créer des bateaux à moteur Bavaria.
Bases de la construction des bateaux
Avant le développement des techniques de construction en fibre de verre, les bateaux étaient construits en bois, en acier et en d’autres matériaux, en assemblant des pièces et des pièces dans une structure qui était ensuite gainée d’une coque. Avec la construction de bateaux en fibre de verre, cependant, les principaux composants du bateau – la coque, le pont, la doublure et les grandes pièces comme les consoles — sont moulés en fibre de verre. Habituellement, cela signifie commencer par un moule femelle. Le moule est d’abord pulvérisé avec du gelcoat, puis un tissu en fibre de verre est appliqué, puis de la résine est utilisée pour saturer ou « mouiller” la fibre de verre. Lorsque la résine durcit, vous avez une coque ou une partie de bateau (pour une explication des différentes parties de bateau, consultez notre Guide du Débutant sur la terminologie du bateau).
Les renforts structurels tels que les longerons et les cloisons peuvent être moulés séparément puis recouverts de fibre de verre sur la pièce, ou peuvent dans certains cas être posés en même temps. Alors que la coque est encore ouverte et exposée, des éléments qui seront situés sous le niveau du pont, comme des réservoirs de carburant et d’eau ou des moteurs intérieurs, peuvent être montés. C’est également le cas lorsque la plomberie et le câblage peuvent être exécutés. Ensuite, les principaux composants sont assemblés. Pour la plupart des bateaux à moteur modernes, cela signifie que le pont et / ou la doublure est soulevé, souvent avec une grue, et abaissé dans la coque.
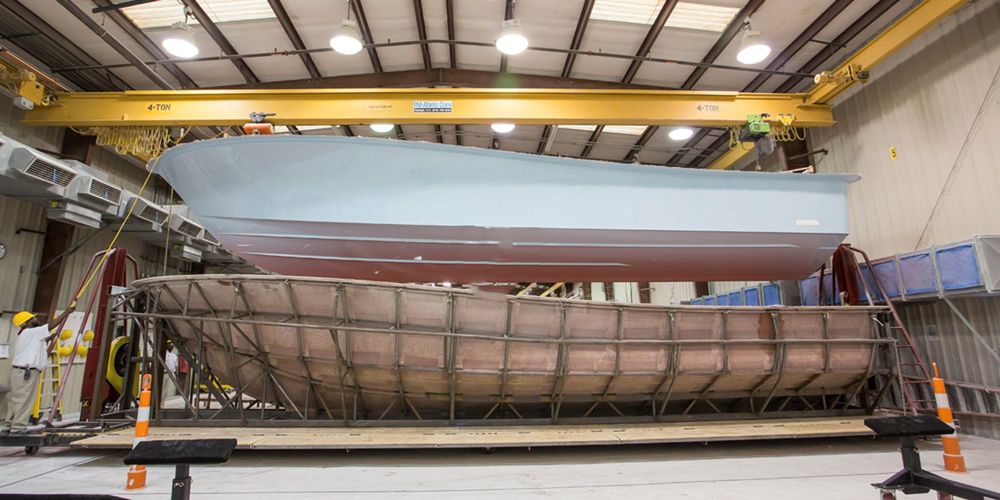
Les ponts roulants sont souvent utilisés pour soulever les principales pièces de bateau, comme cette coque pour un bateau de pêche régulateur, hors des moules et en position pour un assemblage ultérieur.
De nombreux bateaux sont conçus avec un joint ”boîte à chaussures » où la coque et le pont ont des brides d’accouplement, ou se chevauchent. Souvent, des attaches mécaniques telles que des vis ou des boulons traversants sont utilisées pour fixer les pièces ensemble, en plus de l’utilisation d’un agent de liaison chimique et d’un scellant comme le méthacrylate de méthyle ou le 3M 5200, ce qui rend également le joint étanche à l’eau. De plus, certains constructeurs en fibre de verre autour du périmètre du joint coque-pont.
Une fois les principales parties du bateau assemblées, des aménagements intérieurs tels que des sièges et des volants peuvent ensuite être ajoutés. Enfin, les détails et les finitions peuvent être soignés.
Changements dans la façon de construire un bateau
La première révolution dans la construction navale moderne a évidemment été le passage d’une construction principalement en bois à une construction principalement en fibre de verre, mais une seconde a été beaucoup plus subtile. Il y a eu une transition des méthodes conventionnelles de fibre de verre à une foule de matériaux et de techniques exotiques qui peuvent gêner même le plaisancier expérimenté avec des mots à la mode et du jargon.
Le concept reste essentiellement le même, cependant. La fibre de verre (correctement appelée plastique renforcé de fibre de verre, ou PRF) est toujours un matériau fibreux placé dans une substance liante de résine. Dans les toutes premières années, la fibre de verre était littéralement des fibres de verre, mais cela s’est rapidement transformé en fibres de divers plastiques synthétiques. Depuis de nombreuses années, une construction en fibre de verre est faite de tissu, de mèches, de tapis et de résines que vous pouvez acheter dans n’importe quelle quincaillerie. Plus récemment, il est venu à inclure des matériaux plus avancés comme le Kevlar et la fibre de carbone, que beaucoup de gens connaissent grâce à leur utilisation dans d’autres produits. Aujourd’hui, cependant, il y a tellement de matériaux différents utilisés qu’un diplôme en génie chimique est utile lors de la lecture de la brochure pour un nouveau bateau.
Une partie des progrès est venue des efforts des constructeurs de bateaux à moteur de course au large et de voiliers de course au large pour produire des bateaux plus légers, plus solides et donc plus rapides, mais le véritable impact est venu avec la crise énergétique. Étant donné que la fibre de verre est un produit pétrochimique, il était logique pour les constructeurs de bateaux d’étudier des moyens de rendre les bateaux plus légers sans perte de résistance, car chaque livre de fibre de verre éliminée économisait de l’argent au constructeur. Pour les constructeurs de bateaux à moteur, un bateau léger mais solide est également plus économe en carburant.
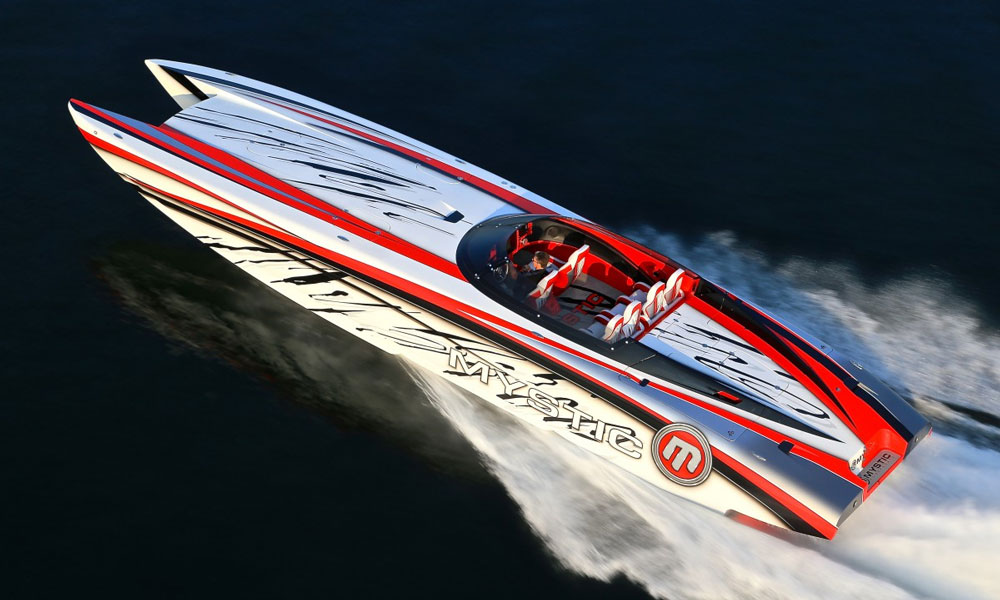
Le développement de bateaux rapides sérieux, comme ce catamaran mystique, a joué un rôle important car les fabricants ont appris à minimiser le poids. Cependant, c’est le coût de la construction qui a stimulé cette tendance chez les constructeurs de bateaux de tous types.
Une grande partie de la recherche et du développement provenait en fait des industries aéronautiques et aérospatiales, où la résistance et la légèreté ont toujours été des préoccupations primordiales, et le ruissellement de la technologie est devenu une telle cascade que de nombreux propriétaires de bateaux ignorent les changements qui se produisent à la fois dans les nouveaux matériaux et les nouvelles techniques de moulage.
Types de résine de fibre de verre
Il existe trois types de résines: polyester, vinylester et époxy. Chacun a sa place dans le monde de la construction navale. Le facteur important est que le constructeur assemble correctement la résine au type de matériau de renforcement utilisé afin que les résistances soient adaptées. Par exemple, une résine vinylester est idéale pour le verre S mais, lorsqu’elle est utilisée avec le verre E, le matériau de renforcement échouera avant la résine.
Polyester:
C’est la résine la plus couramment utilisée pour la construction navale aujourd’hui, et la plupart des propriétaires de bateaux la connaissent bien. Il est peu coûteux et généralement polyvalent. Il a de faibles propriétés d’étirement (allongement), il n’est donc pas utilisé sur les bateaux modernes de haute performance, mais il convient parfaitement à la plupart des bateaux. Le polyester le plus courant est une base orthophtalique, mais les nouveaux polyesters à base isophtalique gagnent en popularité. Les isophtaliques sont plus résistants à l’eau et aux produits chimiques, sont plus résistants à l’abrasion et ont des performances d’impact et de fatigue (flex) plus élevées. La plupart des finitions de gel coat modernes sont fabriquées avec des résines isophtaliques.
Vinylester:
En remplacement du polyester, les vinylesters ont de meilleures caractéristiques d’étirement que les polyesters, ils correspondent donc plus étroitement aux forces des différents renforts exotiques. Le vinylester a également de bonnes propriétés de résistance à l’eau et de fatigue, mais il est plus cher que la résine de polyester. Une caractéristique importante du vinylester est qu’il a une excellente résistance de liaison secondaire, de sorte que les cloisons ou les longerons ajoutés à une coque durcie auront une meilleure liaison que sur une coque en polyester.
Epoxy:
C’est une résine haute performance, avec un prix assorti. Les résines époxydes ont la réputation d’être difficiles à travailler car les premières époxydes étaient épaisses, mais de nombreuses époxydes modernes sont assez liquides. L’époxy adhère mieux que toute autre résine à une large gamme de matériaux, ce qui le rend idéal pour attacher des noyaux, des limons ou d’autres articles.
Types de tissus en fibre de verre
Les tissus utilisant des brins continus sont les tissus les plus courants, avec des poids allant de quatre à 15 onces par mètre carré. Les poids plus lourds, généralement appelés mèches ou mèches tissées, sont constitués de fils de fibres non torsadés dans des poids allant jusqu’à 48 onces par yard. La mèche finie ressemble à une toile de jute grossière et, comme tous les tissus, a une bonne résistance bidirectionnelle. Les poids de tissu plus légers peuvent être trouvés dans une variété de motifs de tissage, tels que le sergé, le satin et le mat, à des fins différentes.
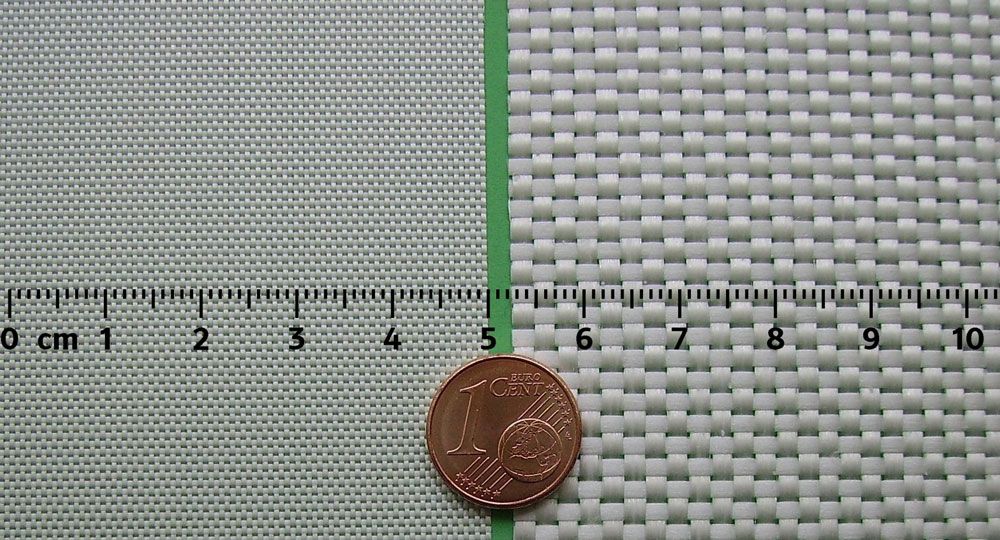
Deux exemples de tissu en fibre de verre: la fibre de verre à gauche est nettement plus fine et plus légère, mais offre moins de rigidité.
E-Glass:
C’est le tissu en fibre de verre le plus couramment utilisé dans la construction navale aujourd’hui. Vous pouvez acheter du verre électronique dans un magasin de fournitures marines et le coller avec de la résine polyester. Il est fabriqué à partir de plastique fondu filé en fines fibres qui sont ensuite soit tissées en tissu, soit rassemblées en mèche.
S-Glass:
Il s’agit d’un tissu en fibre de verre haute performance de l’industrie aéronautique. Il est trois à cinq fois plus cher que le verre électronique, mais il est également beaucoup plus résistant. Développé par Owens-Corning, il a une résistance à la traction, aux chocs et à la flexion 20 à 40% plus élevée que le verre électronique. Il existe deux types de verre S: S-1, qui répond aux normes aérospatiales critiques et coûte aveuglément cher; et S-2, qui est utilisé dans l’industrie maritime. En Europe, le verre S est appelé verre R.
Mat:
Le mat est généralement fait de verre électronique et se compose de fibres aléatoires de deux à trois pouces maintenues en place par un liant soluble dans la résine. Le tapis est utilisé principalement pour l’épaisseur et la rigidité de la construction dans les couches de fibre de verre. Le tapis résiste au « print-through », où le tissage des mèches se manifeste dans la couche extérieure de la coque, mais il absorbe également une énorme quantité de résine et est peu résistant pour son poids.
Fibres unidirectionnelles:
C’est l’une des avancées dans les matériaux de renforcement. Il se compose de brins de fibres allant dans une seule direction, maintenus ensemble par des fibres uniques collées ou cousues latéralement, de la même manière qu’une clôture en bambou est maintenue ensemble par quelques fils. De toute évidence, il a une résistance directionnelle très élevée, de sorte qu’il peut être utilisé dans des zones où les charges sont spécifiques. Parce qu’il n’est pas tissé, il n’y a pas de plis et il est plus facile pour les travailleurs de s’humidifier avec de la résine car il ne retient pas l’air comme un tissu en tissu.
Fibres bi-axiales:
Techniquement, la plupart des tissus sont bi-axiaux, mais la définition moderne signifie un tissu fabriqué à partir de couches de tissus unidirectionnels qui ne sont pas tissées les unes à travers les autres. Une couche se pose simplement au-dessus de la couche suivante pour produire une bande de fibres sans pli.
Fibres tri-axiales:
Il s’agit d’un matériau en couches similaire au tissu bi-axial, sauf que les fibres sont orientées dans trois directions, souvent à 120 degrés les unes par rapport aux autres pour répartir les charges.
Matériaux de construction avancés en fibre de verre
Fibre de carbone:
Ces fibres de graphite offrent une rigidité exceptionnelle ainsi que des résistances à la traction et à la compression élevées et sont souvent utilisées en conjonction avec du verre S ou d’autres exotiques pour fournir une résistance aux chocs acceptable, qui est par ailleurs assez faible. La fibre de carbone est très chère, mais elle peut surpasser le métal dans de nombreuses situations. De nombreuses entreprises produisent de la fibre de carbone dans le monde entier et les utilisations dépendent de la teneur en carbone de la fibre elle-même, certaines étant destinées à des applications à haute résistance et d’autres étant destinées à des situations de module (rigidité) élevé. C’est le type de renfort de fibres le plus cher disponible, coûtant autant par livre que 100 fois le verre électronique commun. Après le Kevlar en termes de résistance spécifique, les fibres de carbone sont supérieures à toute autre fibre en termes de rigidité.
Kevlar :
Nom de marque d’un produit DuPont, il est utilisé pour désigner les fibres d’aramide dont Du Pont est le seul producteur mondial. Un polymide aromatique (généralement abrégé en aramide), le Kevlar est une forme de nylon qui a été initialement développée au milieu des années 1960 en tant que « Fibre B » pour renforcer la ceinture radiale des pneus. Ses propriétés uniques ont rapidement été utilisées dans d’autres utilisations, et le public pense généralement au Kevlar en termes de vestes pare-balles. Il existe en fait deux formes de Kevlar disponibles. Le Kevlar 29 est utilisé pour les lignes, les câbles et les gilets pare-éclats, tandis que le Kevlar 49 est utilisé comme fibre de renforcement dans les composites plastiques. En comparaison de la résistance au poids, le kevlar a la résistance à la traction spécifique la plus élevée de toutes les fibres commerciales. Il est cinq fois plus résistant que l’acier et deux fois plus résistant que le verre électronique, ce qui permet à une coque en Kevlar de conserver la même résistance qu’une coque en verre électronique à une fraction du poids. La résistance aux chocs est également un point fort du Kevlar, et il est capable de résister à des impacts répétés ainsi que de résister à la tendance des autres fibres de renforcement à laisser les fissures se propager. Le côté négatif du Kevlar est une faiblesse marquée de la résistance à la compression, il est donc souvent utilisé en conjonction avec d’autres fibres qui équilibrent ce trait.
Nomex:
Un produit chimique développé par DuPont, le Nomex est surtout célèbre pour ses qualités ignifuges, et il est utilisé dans les combinaisons résistantes au feu pour les pompiers et les conducteurs de voitures de course. C’est un aramide, qui est transformé en une substance semblable à du papier pour une utilisation en nid d’abeille.
Hybrides:
Ce sont des tissus de renforcement qui combinent deux types de fibres différents ou plus. Un hybride commun est un mélange de Kevlar et de fibre de carbone. Le Kevlar offre une résistance élevée aux chocs, tandis que la fibre de carbone fournit la rigidité. Des combinaisons de verre S, de Kevlar et de fibre de carbone sont également disponibles pour optimiser certaines propriétés à un coût minimum.
Matériaux de base avancés
Les matériaux de base sont souvent utilisés pour réduire le poids et augmenter la rigidité. Certains constructeurs centrent l’ensemble du bateau; d’autres construisent avec de la fibre de verre solide à partir de la ligne de flottaison et du carottage au-dessus, et d’autres encore utilisent un mélange de carottage et de verre solide dans tout le bateau.
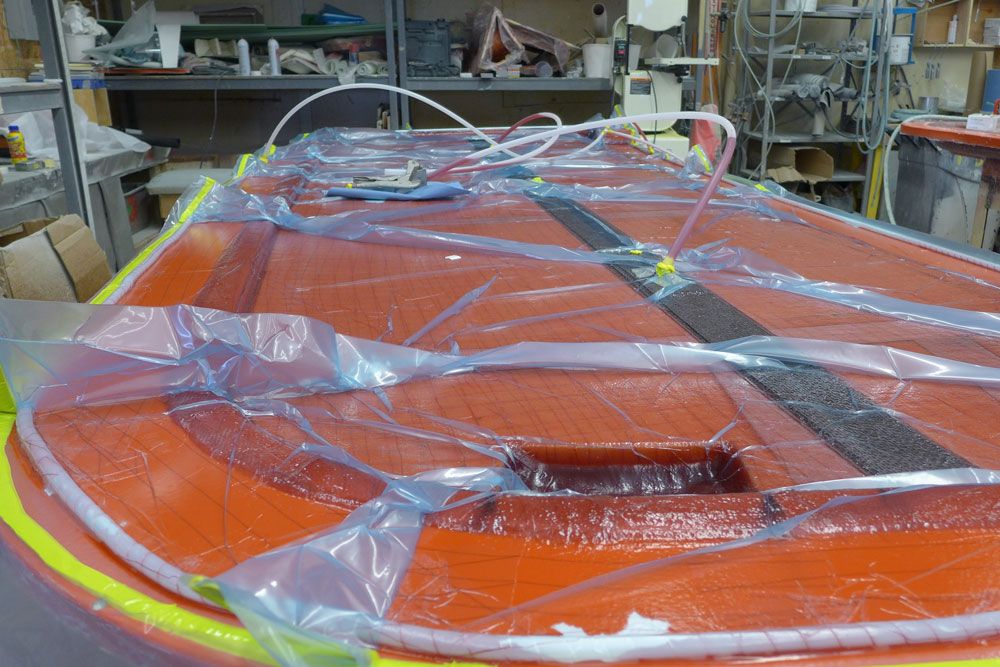
Vous pouvez voir le noyau (à l’aspect damier) dans cette partie, sur le point d’être mis sous vide chez Sabre Yachts. Crédit photo : Sabre Yachts.
Noyau de balsa:
Lors de sa première utilisation comme raidisseur de coque, les constructeurs de bateaux ont posé de longues planches de balsa dans les coques, mais cette méthode a entraîné une pourriture et une défaillance structurelle lorsque l’eau « s’est infiltrée » dans toute la planche. Il a fallu beaucoup de temps au balsa pour vivre ce début, mais le balsa moderne est maintenant un matériau de carottage largement accepté dans les bateaux. La solution est venue de trancher le grain, de le tourner sur le bord et de produire un motif en damier de morceaux de grain final qui ne transmettent pas l’eau. Le résultat est un noyau rigide, léger et peu coûteux avec une bonne qualité d’impact et une résistance à la compression élevée. Une caractéristique supplémentaire est la qualité d’isolation du balsa contre le son, les changements thermiques et les vibrations. Un facteur négatif est que le balsa peut absorber la résine, ce qui alourdit la coque, mais une finition de qualité peut empêcher cela de se produire.
Mousses de PVC:
Airex et Klegecell (prononcé kledge-a-cell) sont les noyaux de mousse les plus populaires produits commercialement et utilisés aujourd’hui. Les deux sont des mousses à cellules fermées fabriquées à partir de chlorure de polyvinyle, mais chacune a des caractéristiques différentes. Airex est un PVC non réticulé, ce qui le rend plus flexible et résistant aux dommages. Klegecell est une mousse réticulée extrêmement rigide. Les bateaux construits à l’étranger utilisent souvent Divinycell, une version scandinave de Klegecell.
Honeycomb:
Honeycomb est exactement ce à quoi il ressemble: un motif de matériau gaufré pour donner la plus grande rigidité à n’importe quel noyau de poids égal. Les résistances à la compression et au cisaillement sont inégalées, ce qui pourrait être attendu d’un matériau utilisé à l’origine dans les aéronefs pour les revêtements de sol et les cloisons. Le nid d’abeille Nomex est le plus souvent trouvé sur les yachts, bien qu’il s’agisse certainement d’une extravagance à prix élevé pour les propriétaires à la recherche de la dernière once d’économies de poids. Assez étonnamment, certains nids d’abeilles sont en papier. Un papier kraft est imprégné de résines puis formé en nid d’abeille, ce qui le rend résistant à l’eau et robuste, mais le nid d’abeille en papier est plus lourd que le Nomex. Les « panneaux à peau » sont des feuilles de nid d’abeille prêtes à l’emploi ressemblant à un morceau de contreplaqué, et sont disponibles avec du placage de teck ou diverses autres superpositions qui peuvent être découpées en cloisons en nid d’abeille prêtes à l’emploi.
Obtenez un aperçu du fonctionnement du noyau à l’intérieur d’une pièce en fibre de verre en regardant notre vidéo sur la construction de bateaux fourrés en mousse.
Techniques avancées de construction de bateaux
Parallèlement à ces nouveaux matériaux, les méthodes de mise en place de ce qui deviendra éventuellement un bateau ont également progressé ces dernières années. Encore une fois, minimiser le poids tout en maximisant la force est pratiquement toujours l’objectif.
Ensachage sous vide
: Ce processus commence comme une couche de moulage ouverte, mais le stratifié humide est enfermé dans un film plastique et un vide est appliqué pour extraire l’excès de résine. L’excès de résine n’ajoute pas de résistance – c’est à cela que sert la fibre de verre – mais cela ajoute du poids. Ainsi, le processus d’ensachage sous vide réduit le poids éventuel du bateau sans sacrifier la résistance.
Infusion sous vide
: Le procédé d’infusion sous vide incorpore de la même manière un film plastique et un vide pour atteindre un rapport résine/verre idéal. Cependant, plutôt que de commencer par une pose humide, le vide, avec un ensemble de lignes d’alimentation en résine, introduit et attire la résine à travers le tissu en premier lieu. Cela permet une mesure plus précise des matériaux et la possibilité d’appliquer une pression uniforme sur une grande surface, de sorte que vous pouvez poser des pièces plus grandes.
Pour une explication simplifiée du fonctionnement du processus de vide lors du moulage des bateaux, regardez notre vidéo Comprendre l’ensachage sous vide.
Méthodes alternatives de construction de bateaux
Bien que la grande majorité des bateaux de plaisance construits aujourd’hui reposent sur ces matériaux et méthodes, il existe des exceptions. Le plus souvent, vous les trouverez avec de grands yachts, où le prix n’est pas un objet. Certains sont encore construits avec des coques métalliques, et d’autres avec des techniques comme le « moulage à froid” ou la « planche sur cadre ». »Dans ces cas, la structure du bateau est fabriquée à partir de bois qui est ensuite recouvert ou encapsulé de fibre de verre et de résine époxy posés à la main. Les yachts de pêche sportive comme un cabriolet Bayliss de 73 pieds, et les croiseurs haut de gamme comme les yachts Vicem, sont construits avec ces méthodes.
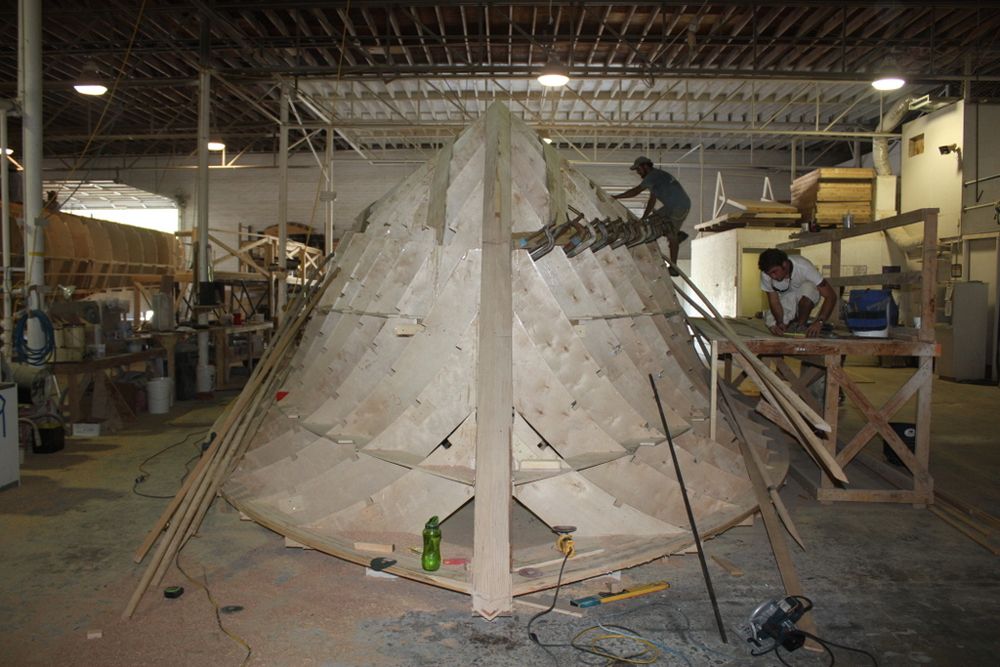
Bien que de nombreux constructeurs de bateaux modernes évitent l’utilisation du bois, sur des yachts personnalisés haut de gamme comme cette baie de Jarrett, des méthodes telles que le moulage à froid sont souvent considérées comme supérieures aux techniques plus modernes.
À l’extrémité opposée de l’extrême, vous avez des bateaux en PRF sans le F ou le R et seulement le P–plastique. Bien que les plus grands bateaux tout en plastique en production mesurent moins de 20 pieds de longueur (et la plupart sont inférieurs à 12 ou 14 pieds), le plastique rotomoulé est devenu très populaire sur les marchés du kayak et du dériveur. Ces engins simples et peu coûteux sont formés de pastilles de plastique qui sont fondues à l’intérieur d’un four rotatif, qui est également un moule. Quand il refroidit, le plastique a pris la forme du moule et un bateau sort.
Maintenant que vous connaissez les bases de la construction navale moderne et que vous êtes prêt à choisir votre propre bateau, assurez-vous de lire Comment acheter un bateau: Conseils pour les premiers acheteurs.
Note de l’éditeur: Cet article intègre des parties d’un article de base sur la construction de bateaux de Chris Caswell, d’août 2000, et a été mis à jour en octobre 2018 et mars 2020.