Bådbygning: grundlæggende konstruktion af harpiks, glasfiber og kerner
mange mennesker spekulerer på, hvordan moderne glasfiberbåde er bygget, og bådbygning i dag er slet ikke som det var tilbage, da antikke og klassiske motorbåde blev bygget. Disse dage, båd bygning er faktisk temmelig high-tech.
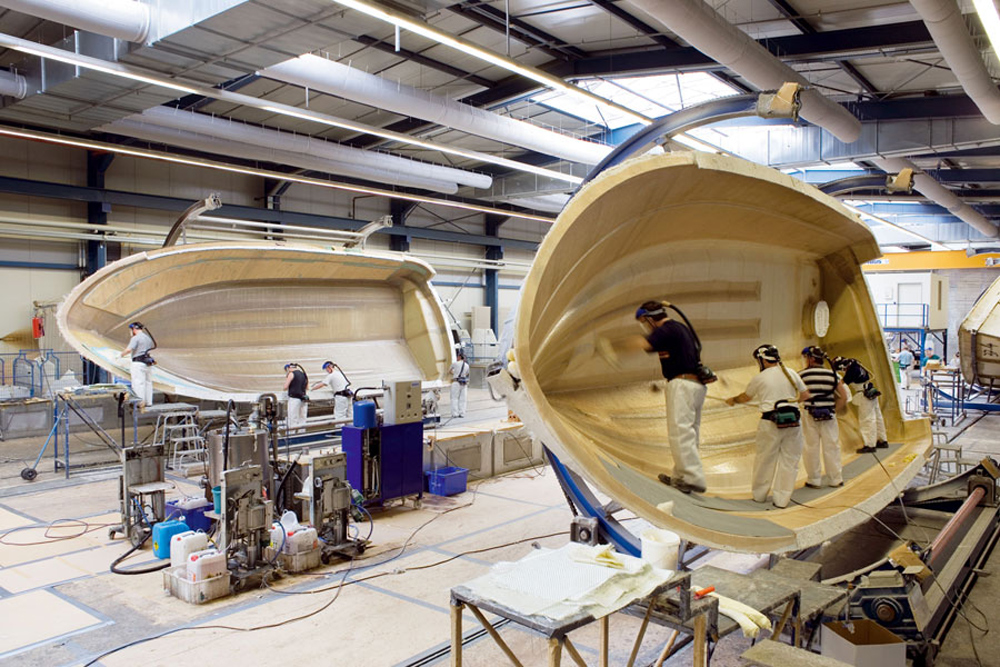
i den moderne tidsalder begynder bygning af en båd med en form. Disse vil blive brugt til at skabe Bayern motorbåde.
grundlæggende om bådbygning
før udviklingen af fiberglaskonstruktionsteknikker blev både bygget af træ, stål og andre materialer ved at samle stykker og dele i en struktur, der derefter blev beklædt med et skrog. Med glasfiber båd bygning, imidlertid, de vigtigste komponenter i båden – skroget, dæk, liner, og store dele som konsoller—er støbt af glasfiber. Normalt betyder det at starte med en kvindelig skimmel. Formen sprøjtes først med gelcoat, derefter påføres glasfiberklud, og derefter bruges harpiks til at mætte eller “våde” glasfiberen. Når harpiksen hærder, har du et skrog eller en båddel (for en forklaring af de forskellige båddele, se vores Begyndervejledning til Bådterminologi).
strukturelle forstærkninger som stringere og skotter kan støbes separat og derefter fiberglas til delen, eller kan i nogle tilfælde lægges op på samme tid. Mens skroget stadig er åbent og udsat, kan genstande, der vil være placeret under dækniveau som brændstof-og vandtanke eller indenbords motorer, monteres. Dette er også, når VVS og ledninger kan køres. Derefter samles de vigtigste komponenter. For de fleste moderne motorbåde betyder det, at dækket og / eller foringen løftes, ofte med en kran, og sænkes ned i skroget.
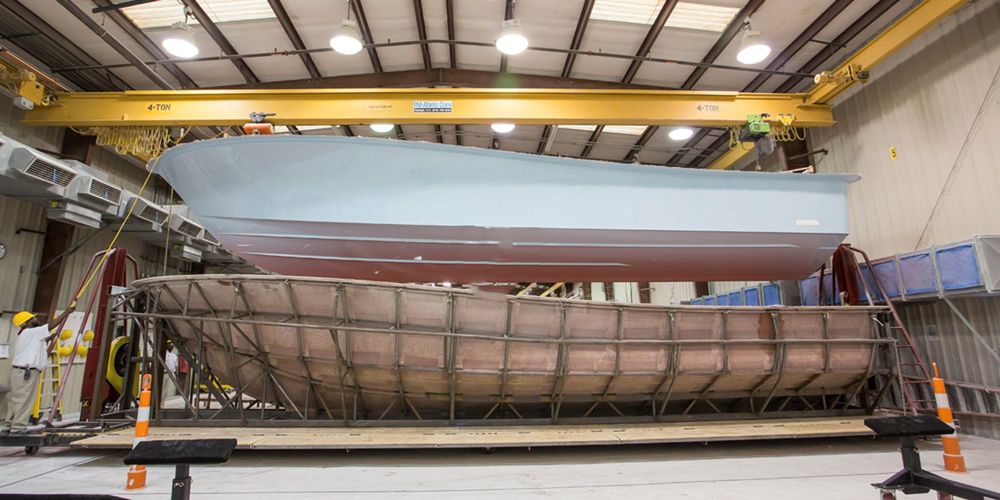
Overhead kraner bruges ofte til at løfte store båddele, som dette skrog til en Regulator fiskerbåd, ud af formene og i position til yderligere montering.
mange både er designet med en “skoboks”-samling, hvor skroget og dækket har parringsflanger eller overlapper hinanden. Ofte bruges mekaniske fastgørelseselementer såsom skruer eller gennemgående bolte til at fastgøre delene sammen ud over brugen af et kemisk bindemiddel og tætningsmiddel som methylmethacrylat eller 3M 5200, hvilket også gør samlingen vandtæt. Derudover nogle bygherrer glasfiber omkring omkredsen af skroget til dæk fælles.
med de store dele af båden samlet, kan indvendige fittings som sæder og rat derefter tilføjes. Endelig kan detaljerne og sidste hånd tages hånd om.
ændringer i hvordan man bygger en båd
Den første revolution i moderne bådebygning var åbenlyst skiftet fra for det meste træ til for det meste glasfiberkonstruktion, men en anden har været meget mere subtil. Der har været en overgang fra konventionelle glasfibermetoder til en række eksotiske materialer og teknikker, der kan befuddle selv den erfarne lystsejler med brusord og jargon.
konceptet er dog stort set det samme. Glasfiber (korrekt kaldet glasfiberforstærket plast eller FRP) er stadig et fibermateriale, der er sat i et bindende stof af harpiks. I de meget tidlige år var glasfiber bogstaveligt talt glasfibre, men det skiftede snart til fibre af forskellige syntetiske plastmaterialer. I mange år har en glasfiberkonstruktion været fra klud, roving, mat og harpikser, du kan købe i enhver isenkræmmer. For nylig kom det til at omfatte mere avancerede materialer som Kevlar og kulfiber, som mange mennesker er bekendt med fra deres anvendelse i andre produkter. I dag er der dog så mange forskellige materialer, der bruges, at en grad i Kemiteknik er nyttig, når man læser brochuren til en ny båd.
nogle af fremskridtene kom fra bestræbelserne fra bygherrer af offshore racing motorbåde og ocean racing sejlbåde til at producere lettere, stærkere og derfor hurtigere både, men den virkelige effekt kom med energikrisen. Da glasfiber er et petrokemisk produkt, var det fornuftigt for bådebyggere at undersøge måder at gøre både lettere uden tab af styrke, fordi hvert pund glasfiber elimineret sparede bygherrens penge. For motorbådbyggere er en let, men stærk båd også mere brændstofeffektiv.
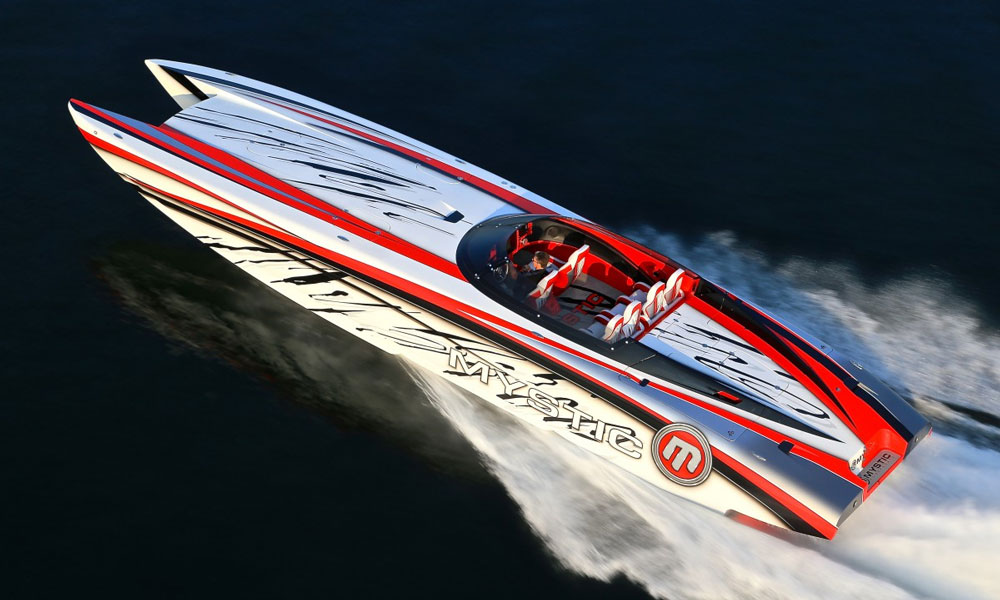
udviklingen af seriøse speedbåde, som denne mystiske katamaran, spillede en vigtig rolle, da producenterne lærte at minimere vægten. Det var imidlertid omkostningerne ved byggeri, der ansporede til denne tendens blandt bådebyggere af alle typer.
meget af forskningen og udviklingen kom faktisk fra fly-og luftfartsindustrien, hvor styrke og let vægt altid har været primære bekymringer, og teknologiens nedstrømning er blevet et sådant vandfald, at mange bådejere ikke er opmærksomme på de ændringer, der finder sted i både nye materialer og nye støbeteknikker.
typer af glasfiberharpiks
der er tre typer harpikser: polyester, vinylester og Epoksi. Hver har en plads i bådbygningsverdenen. Den vigtige faktor er, at bygherren korrekt matcher harpiksen til den type forstærkningsmateriale, der anvendes, så styrkerne matches. For eksempel er en vinylesterharpiks ideel til S-glas, men når det bruges sammen med E-glas, vil det forstærkende materiale svigte før harpiksen.
Polyester:
Dette er den harpiks, der oftest bruges til bådebygning i dag, og de fleste bådejere er bekendt med det. Det er billigt og generelt til alle formål. Det har lave strækningsegenskaber (forlængelse), så det bruges ikke på moderne højtydende både, men det er helt passende for de fleste både. Den mest almindelige polyester er en orthophthalic base, men nyere isophthalic baserede polyestere vinder i popularitet. Isophthalics er mere modstandsdygtige over for vand og kemikalier, er mere slidbestandige og har højere effekt og træthed (bøjning). De fleste moderne gelcoat finish er lavet med isophthalharpikser.
Vinylester:
En alternativ til polyester, vinylestere har bedre strækegenskaber end polyestere, så de passer tættere sammen med styrkerne ved de forskellige eksotiske forstærkninger. Vinylester har også god vandmodstand og træthedsegenskaber, men det er dyrere end polyesterharpiks. Et vigtigt træk ved vinylester er, at det har fremragende sekundær bindingsstyrke, så skotter eller stringere føjet til et hærdet skrog vil have en bedre binding end på et polyesterskrog.
Epoksi:
Dette er højtydende harpiks, med en matchende pris. Har haft et ry for at være svært at arbejde siden tidlige epokser var tyk, men mange moderne epokser er ganske flydende. Den klæber bedre end nogen anden harpiks til en lang række materialer, hvilket gør den ideel til fastgørelse af kerner, stringere eller andre genstande.
typer af glasfiberdug
vævede stoffer ved hjælp af kontinuerlige tråde er de mest almindelige klude med vægte fra fire til 15 ounces pr. Tungere vægte, normalt kaldet roving eller vævet roving, består af snoet garn af fiber i vægte, der spænder op til 48 ounces pr. Den færdige roving ligner en grov jute og har ligesom alle klæder god tovejsstyrke. De lettere klud vægte kan findes i en række vævning mønstre, såsom bindinger, satin og mat, til forskellige formål.
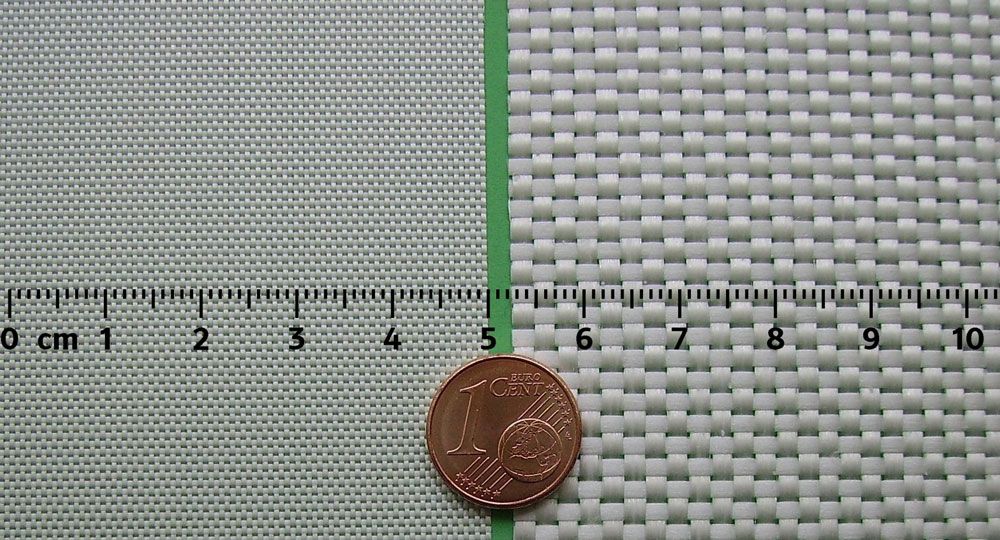
to eksempler på glasfiberdug: glasfiberen til venstre er betydeligt tyndere og lettere, men giver mindre stivhed.
E-glas:
Dette er den mest anvendte glasfiberdug i bådebygning i dag. Du kan købe E-glas i en marine forsyningsbutik og binde det med polyesterharpiks. Den er lavet af smeltet plast spundet i fine fibre, som derefter enten er vævet ind i klud eller løst samlet i roving.
S-glas:
Dette er højtydende glasfiberdug fra flyindustrien. Det er tre til fem gange dyrere end E-glas, men det er også meget stærkere. Den har 20 Til 40 procent højere trækstyrke, slagstyrke og bøjningsstyrke end E-glas. Der er to typer S-glas: S-1, der opfylder kritiske luftfartsstandarder og er blændende dyre; og S-2, der bruges i marineindustrien. I Europa kaldes S-glas R-glas.
Mat:
Mat er normalt lavet af E-glas og består af tilfældige to til tre tommer fibre, der holdes på plads af et bindemiddel, der er harpiksopløseligt. Mat bruges primært til at opbygge tykkelse og stivhed i glasfiber layups. Mat modstår “print-through”, hvor vævningen af roving viser sig i skrogets ydre lag, men det opsuger også en enorm mængde harpiks og har lav styrke for sin vægt.
Uni-Directional fibre:
Dette er et af fremskridtene inden for forstærkende materialer. Den består af tråde af fiber, der kun løber i en retning, holdes sammen af enkeltfibre, der limes eller sys sideværts, meget på samme måde som et bambushegn holdes sammen af et par ledninger. Det har naturligvis meget høj retningsstyrke, så det kan bruges i områder, hvor belastningerne er specifikke. Fordi det ikke er vævet, er der ingen kinks, og det er lettere for arbejderne at vådte ud med harpiks, da det ikke holder luft som et kludstof.
biaksiale fibre:
teknisk set er det meste stof biaksialt, men den moderne definition betyder et stof fremstillet af lag af ensrettet klud, der ikke er vævet gennem hinanden. Et lag ligger simpelthen oven på det næste lag for at producere et kink-frit bånd af fiber.
triaksiale fibre:
Dette er et lagdelt materiale, der ligner biaksial klud, bortset fra at fibrene er orienteret i tre retninger, ofte ved 120 grader til hinanden for at sprede belastningerne.
avancerede glasfiber byggematerialer
kulfiber:
disse fibre af grafit giver fremragende stivhed såvel som høje træk-og kompressionsstyrker og bruges ofte sammen med S-glas eller andre eksotiske stoffer for at give acceptabel slagfasthed, som ellers er ret lav. Kulfiber er meget dyrt, men det kan overgå metal i mange situationer. Mange virksomheder producerer kulfiber over hele verden, og brugen afhænger af kulstofindholdet i selve fiberen, hvor nogle er beregnet til applikationer med høj styrke, og andre er rettet mod situationer med høj modul (stivhed). Det er den dyreste type fiberforstærkning til rådighed, der koster så meget pr.pund som 100 gange almindeligt E-glas. Andet kun for Kevlar i specifik styrke er kulfibre bedre end enhver anden fiber i stivhed.
Kevlar:
det varemærkebeskyttede navn for et DuPont-produkt, det bruges til at henvise til aramidfibre, hvoraf Du Pont er den eneste producent over hele verden. En aromatisk polymid (normalt forkortet til aramid), Kevlar er en form for nylon, der oprindeligt blev udviklet i midten af 1960 ‘ erne som “Fiber B” for at forstærke radialdækbælte. Det er unikke egenskaber snart blev sat i andre anvendelser, og offentligheden normalt tænker på Kevlar i form af skudsikre jakker. Der er faktisk to former for Kevlar til rådighed. Kevlar 29 bruges til linjer, kabler og flakjakker, mens Kevlar 49 bruges som forstærkningsfiber i plastkompositter. På en styrke til vægt sammenligning, Kevlar har den højeste specifikke trækstyrke af enhver kommerciel fiber. Det er fem gange stærkere end stål og dobbelt så stærkt som E-glas, hvilket gør det muligt for et Kevlar-skrog at opretholde den samme styrke som et e-glasskrog til en brøkdel af vægten. Slagstyrke er også en Kevlar forte, og den er i stand til at modstå gentagne påvirkninger såvel som modstå tendensen hos andre forstærkende fibre for at tillade revner at sprede sig. Den negative side af Kevlar er en markant svaghed i kompressionsstyrke, så det bruges ofte sammen med andre fibre, der afbalancerer dette træk.
Nomeks:
et kemikalie udviklet af DuPont, Nomeks er mest berømt for sine brandsikre kvaliteter, og det bruges i brandsikre dragter til brandmænd og racerbilchauffører. Det er en aramid, som omdannes til et papirlignende stof til brug i honningkage.
hybrider:
disse er forstærkende stoffer, der kombinerer to eller flere forskellige typer fibre. En almindelig hybrid er en blanding af Kevlar med kulfiber. Kevlar giver høj slagfasthed, mens kulfiberen leverer stivheden. Kombinationer af S-glas, Kevlar og kulfiber er også tilgængelige for at optimere visse egenskaber til minimale omkostninger.
avancerede kernematerialer
kernematerialer bruges ofte til at reducere vægten og øge stivheden. Nogle bygherrer kerne hele båden; andre konstruerer med solid glasfiber fra vandlinjen ned og udkerning ovenfor, og stadig andre bruger en blanding af udkerning og solidt glas i hele båden.
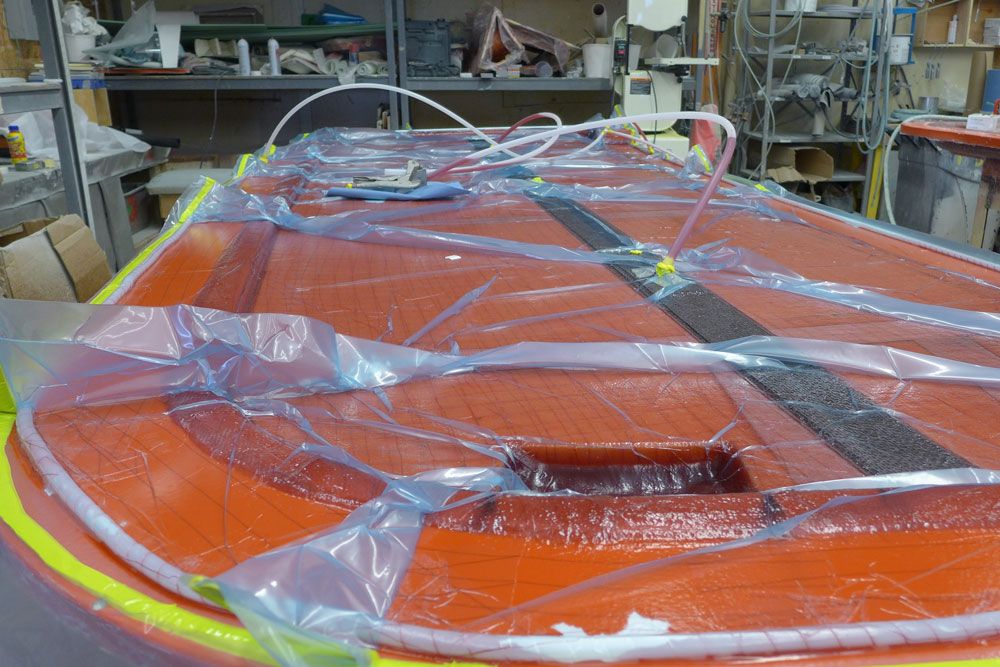
Du kan se kernen (med rutet udseende) i denne del, ved at blive vakuumpakket på Sabre Yachts. Foto Kredit: Sabre Yachts.
Balsa Core:
når først brugt som en skrog afstivning båd bygherrer lagde lange planker af balsa ind i skroget, men denne metode førte til råd og strukturelle svigt, når vand “onde” gennem hele planken. Det har taget balsa lang tid at leve ned i denne begyndelse, men moderne balsa er nu et bredt accepteret kernemateriale i både. Løsningen kom fra at skære gennem kornet, dreje det på kanten og producere et skakternet mønster af endekornstykker, der ikke transmitterer vand. Resultatet er en stiv, let og billig kerne med god slagkvalitet og høj trykstyrke. En ekstra funktion er isoleringskvaliteten af balsa mod lyd, termisk ændring og vibrationer. En negativ faktor er, at balsa kan absorbere harpiks, hvilket gør skroget tungere, men kvalitetshåndtering kan forhindre, at det sker.
PVC skum:
luft og Klegecell (udtales kledge-a-cell) er de mest populære kommercielt producerede skumkerner, der anvendes i dag. Begge er lukkede celleskum fremstillet af polyvinylchlorid, men hver har forskellige egenskaber. Aireks er en ikke tværbundet PVC, hvilket gør den mere fleksibel og modstandsdygtig over for skader. Klegecell er et tværbundet skum, der er ekstremt stift. Udenlandske både bruger ofte Divinycell, en skandinavisk version af Klegecell.
Honeycomb:
Honeycomb er lige, hvad det lyder som: en vaffel-lignende mønster af materiale til at give den højeste stivhed af enhver kerne af samme vægt. Kompressions-og forskydningsstyrkerne er uden sidestykke, hvilket kan forventes af et materiale, der oprindeligt blev brugt i fly til gulve og skotter. Nomek honeycomb er den mest almindeligt forekommende på lystbåde, selvom det bestemt er en ekstravagance med høj billet for ejere på jagt efter den sidste ounce af vægtbesparelser. Overraskende nok er nogle honningkager lavet af papir. Et kraftpapir imprægneres med harpikser og formes derefter til en honningkage, hvilket gør det vandtæt såvel som robust, men papirhoneycomb er tungere end Nomeks. “Skinned paneler” er færdige plader af honningkage, der ligner et stykke krydsfiner, og fås med teakfiner eller forskellige andre overlejringer, der kan skæres i færdige honningkageskotter.
få et indblik i, hvordan core fungerer inde i en glasfiber del ved at se vores forståelse skum Cored båd konstruktion video.
avancerede Bådbygningsteknikker
sammen med disse nye materialer er metoder til at lægge dem op i, hvad der til sidst bliver en båd, også avanceret i de senere år. Igen er minimering af vægten, mens maksimering af styrke næsten altid målet.
vakuumpakning
: denne proces begynder som en åben støbeform, men det våde laminat er lukket i en plastfilm, og der påføres et vakuum for at trække overskydende harpiks ud. Overskydende harpiks tilføjer ikke styrke – det er hvad glasfiber er til – men det tilføjer vægt. Så vakuumposeprocessen reducerer bådens eventuelle vægt uden at ofre nogen styrke.
Vakuuminfusion
: vakuuminfusionsprocessen inkorporerer ligeledes plastfilm og et vakuum for at opnå et ideelt forhold mellem harpiks og glas. Imidlertid, snarere end at begynde med en våd lægge vakuumet, sammen med et sæt harpiksfodringslinjer, introducerer og trækker harpiksen gennem kluden i første omgang. Dette giver mulighed for en mere præcis måling af materialerne og evnen til at anvende jævnt tryk over et stort område, så du kan lægge større dele op.
for en forenklet forklaring af, hvordan vakuum processen fungerer, når støbning både, se vores forståelse vakuum sække video.
Alternative Bådbyggemetoder
mens langt de fleste fritidsbåde, der er bygget i dag, er afhængige af disse materialer og metoder, er der undtagelser. Oftest vil du finde dem med store lystbåde, hvor prisen er ingen genstand. Nogle er stadig bygget med metalskrog, og nogle andre med teknikker som “koldstøbning,” eller “plank på ramme.”I disse tilfælde er bådens struktur Udformet af træ, som derefter er lagdelt med eller indkapslet i håndlagt glasfiber og epoksisharpiks. Sportfishing yachts som en Bayliss 73 fod cabriolet, og high-end krydsere som Vicem yachts, er bygget med disse metoder.
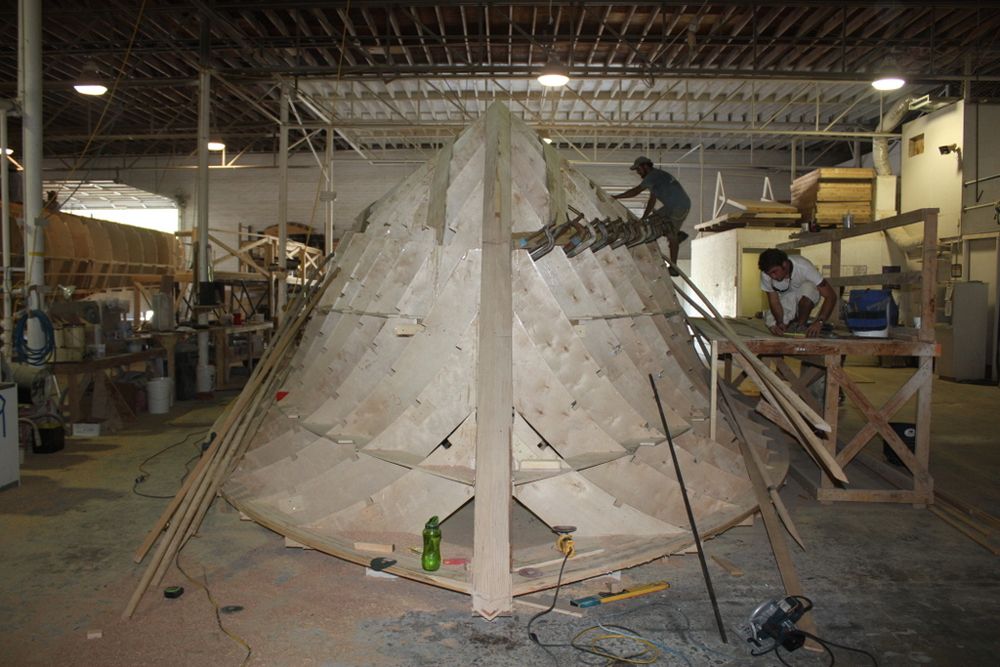
selvom mange moderne bådebyggere undgår brugen af træ, på avancerede brugerdefinerede lystbåde som denne Jarrett Bay, betragtes metoder som koldstøbning ofte bedre end mere moderne teknikker.
i den modsatte ende af det ekstreme har du FRP – både uden F eller R og kun P-plast. Selvom de største all-plast både i produktionen er under 20 fod i længden (og de fleste er under 12 eller 14 fod) roto-støbt plast er blevet meget populært i kajak og jolle markeder. Disse enkle, billige håndværk er dannet af plastpiller, der smeltes ned inde i en roterende ovn, som også er en form. Når det køler af, har plasten taget formens form, og en båd springer ud.
nu hvor du kender det grundlæggende i moderne bådbygning, og du er klar til at vælge en egen båd, skal du læse Sådan køber du en båd: Tips til første gang købere.Redaktørens Note: Denne artikel indeholder dele af en grundlæggende Bådkonstruktionsartikel fra August 2000 og blev opdateret i Oktober 2018 og marts 2020.
kunne lide det? Del det!
- kvidre