Construcción de barcos: Construcción básica de Resina, fibra de vidrio y núcleos
Muchas personas se preguntan cómo se construyen los barcos modernos de fibra de vidrio, y la construcción de barcos hoy en día no es para nada como cuando se construyeron barcos a motor antiguos y clásicos. Hoy en día, la construcción de barcos es bastante de alta tecnología.
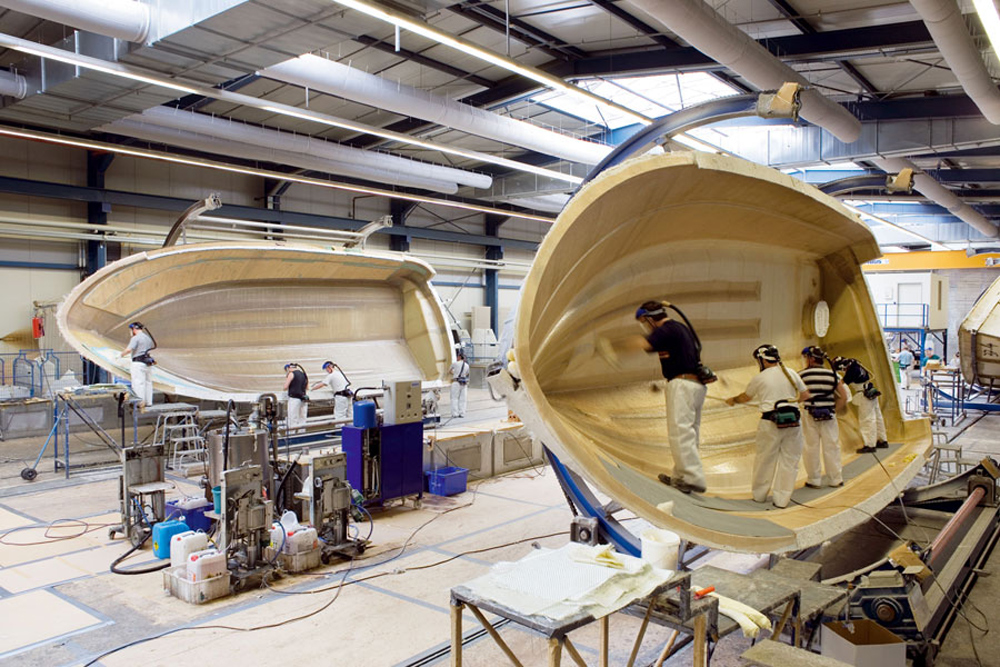
En la era moderna, la construcción de un barco comienza con un molde. Estos se utilizarán para crear barcos de motor Bavaria.
Conceptos básicos de construcción de barcos
Antes del desarrollo de técnicas de construcción de fibra de vidrio, los barcos se construían de madera, acero y otros materiales, ensamblando piezas y piezas en una estructura que luego se enfundaba con un casco. Con la construcción de barcos de fibra de vidrio, sin embargo, los componentes principales del barco, el casco, la cubierta, el revestimiento y las partes grandes como consolas, están moldeados de fibra de vidrio. Por lo general, esto significa comenzar con un molde femenino. El molde se rocía primero con gelcoat, luego se aplica un paño de fibra de vidrio y luego se usa resina para saturar o «mojar» la fibra de vidrio. Cuando la resina se cura, tiene un casco o una parte de barco (para obtener una explicación de las diferentes partes de barco, consulte nuestra Guía para principiantes de Terminología de barco).Los refuerzos estructurales como largueros y mamparos se pueden moldear por separado y luego enfibrar a la pieza, o en algunos casos se pueden colocar al mismo tiempo. Mientras el casco sigue abierto y expuesto, se pueden montar elementos que se ubicarán debajo del nivel de la cubierta, como tanques de combustible y agua o motores internos. Esto también es cuando se puede ejecutar la plomería y el cableado. Luego se ensamblan los componentes principales. Para la mayoría de los barcos de motor modernos, eso significa que la cubierta y/o el revestimiento se levantan, a menudo con una grúa, y se bajan al casco.
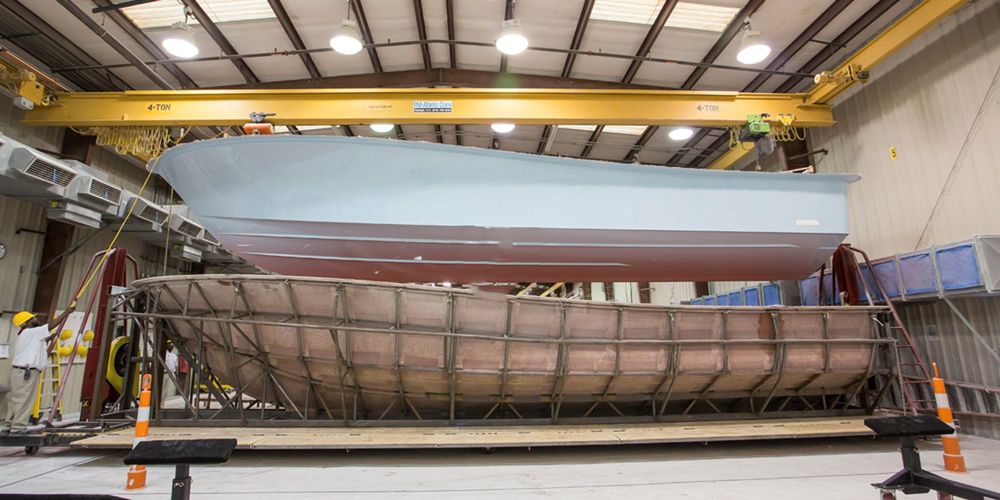
Las grúas aéreas se utilizan a menudo para levantar piezas principales de embarcaciones, como este casco para un barco de pesca Regulador, fuera de los moldes y en su posición para un montaje posterior.
Muchos barcos están diseñados con una junta de «caja de zapatos» donde el casco y la cubierta tienen bridas de acoplamiento, o se superponen entre sí. A menudo, se utilizan sujetadores mecánicos, como tornillos o pernos pasantes, para asegurar las piezas juntas, además del uso de un agente de unión química y sellador como metacrilato de metilo o 3M 5200, que también hace que la junta sea hermética. Además, algunos constructores de fibra de vidrio alrededor del perímetro del casco a la junta de cubierta.Con las partes principales del barco ensambladas, se pueden agregar accesorios interiores como asientos y volantes. Por último, se pueden cuidar los detalles y los toques finales.
Cambios en la forma de construir un barco
La primera revolución en la construcción de barcos moderna fue obviamente el cambio de la construcción en su mayoría de madera a la construcción en su mayoría de fibra de vidrio, pero una segunda ha sido mucho más sutil. Ha habido una transición de los métodos convencionales de fibra de vidrio a una gran cantidad de materiales y técnicas exóticas que pueden confundir incluso al navegante experimentado con palabras de moda y jerga.Sin embargo, el concepto sigue siendo esencialmente el mismo. La fibra de vidrio (propiamente llamada Plástico Reforzado con fibra de Vidrio, o FRP) sigue siendo un material de fibra dentro de una sustancia aglutinante de resina. En los primeros años, la fibra de vidrio era literalmente fibras de vidrio, pero pronto cambió a fibras de varios plásticos sintéticos. Durante muchos años, una construcción de fibra de vidrio ha sido de tela, mecha, estera y resinas que puede comprar en cualquier ferretería. Más recientemente, llegó a incluir materiales más avanzados como Kevlar y fibra de carbono, que muchas personas conocen por su uso en otros productos. Hoy en día, sin embargo, se utilizan tantos materiales diferentes que un título en ingeniería química es útil al leer el folleto para un barco nuevo.
Algunos de los avances vinieron de los esfuerzos de los constructores de lanchas de motor de alta mar y veleros de carreras oceánicas para producir barcos más ligeros, más fuertes y, por lo tanto, más rápidos, pero el impacto real vino con la crisis energética. Dado que la fibra de vidrio es un producto petroquímico, tenía sentido que los constructores de barcos investigaran formas de hacer barcos más livianos sin pérdida de resistencia, porque cada libra de fibra de vidrio eliminada le ahorraba dinero al constructor. Para los constructores de barcos de motor, un barco ligero pero fuerte también es más eficiente en combustible.
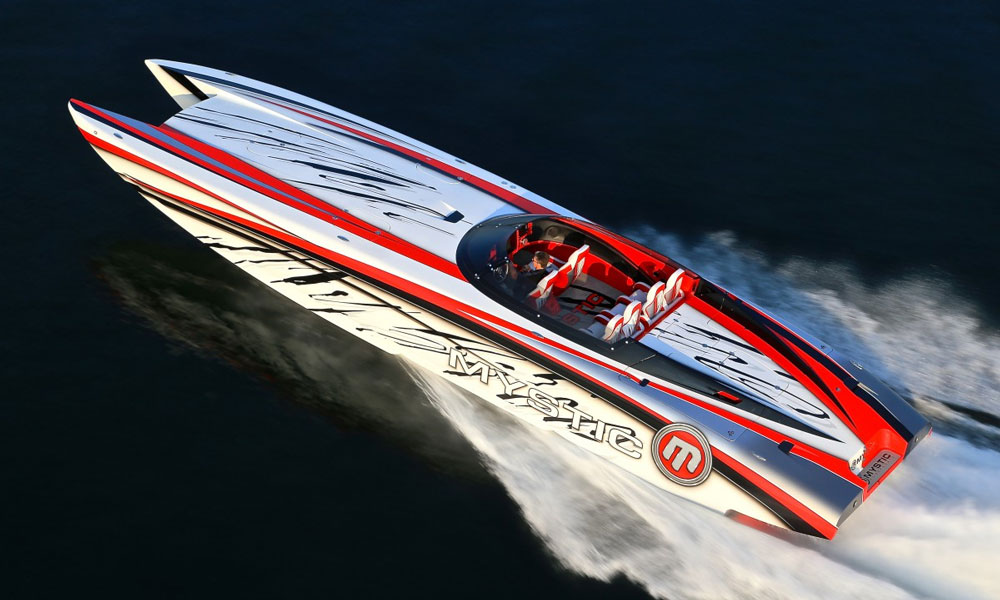
El desarrollo de lanchas rápidas serias, como este catamarán Místico, jugó un papel importante ya que los fabricantes aprendieron a minimizar el peso. Sin embargo, fue el costo de la construcción lo que impulsó esta tendencia entre los constructores de barcos de todo tipo.
Gran parte de la investigación y el desarrollo en realidad provino de las industrias aeronáutica y aeroespacial, donde la resistencia y el peso ligero siempre han sido las principales preocupaciones, y el goteo de la tecnología se ha convertido en una cascada tal que muchos propietarios de barcos no son conscientes de los cambios que tienen lugar tanto en los nuevos materiales como en las nuevas técnicas de moldeo.
Tipos de Resina de Fibra de vidrio
Hay tres tipos de resinas: poliéster, viniléster y epoxi. Cada uno tiene un lugar en el mundo de la construcción de barcos. El factor importante es que el constructor haga coincidir correctamente la resina con el tipo de material de refuerzo que se está utilizando para que las resistencias coincidan. Por ejemplo, una resina de éster de vinilo es ideal para vidrio S, pero, cuando se usa con vidrio E, el material de refuerzo fallará antes que la resina.
Poliéster:
Esta es la resina más utilizada hoy en día para la construcción de embarcaciones, y la mayoría de los propietarios de embarcaciones están familiarizados con ella. Es barato y generalmente de uso múltiple. Tiene propiedades de bajo estiramiento (alargamiento), por lo que no se usa en barcos modernos de alto rendimiento, pero es perfectamente adecuado para la mayoría de los barcos. El poliéster más común es una base ortoftálica, pero los poliésteres con base isoftálica más nuevos están ganando popularidad. Los isoftálicos son más resistentes al agua y a los productos químicos, son más resistentes a la abrasión y tienen un mayor rendimiento de impacto y fatiga (flex). La mayoría de los acabados de gel coat modernos están hechos con resinas isoftálicas.
Viniléster:
Como alternativa al poliéster, los vinilésteres tienen mejores características de estiramiento que los poliésteres, por lo que coinciden más estrechamente con las fortalezas de los diversos refuerzos exóticos. El éster de vinilo también tiene buenas propiedades de resistencia al agua y fatiga, pero es más caro que la resina de poliéster. Una característica importante del éster de vinilo es que tiene una excelente resistencia de unión secundaria, por lo que los mamparos o largueros agregados a un casco curado tendrán una mejor unión que en un casco de poliéster.
Epoxi:
Esta es una resina de alto rendimiento, con un precio a juego. Las resinas epoxi han tenido la reputación de ser difíciles de trabajar desde que los primeros epóxidos eran gruesos, pero muchos epóxidos modernos son bastante líquidos. El epoxi se adhiere mejor que cualquier otra resina a una amplia gama de materiales, lo que lo hace ideal para unir núcleos, largueros u otros artículos.
Los tipos de tela de fibra de vidrio
Las telas tejidas que usan hebras continuas son las telas más comunes, con pesos que van de cuatro a 15 onzas por yarda cuadrada. Los pesos más pesados, generalmente llamados móviles o móviles tejidos, consisten en hilos de fibra sin torsión en pesos que varían hasta 48 onzas por yarda. La mecha terminada se asemeja a una arpillera gruesa y, como todos los paños, tiene una buena resistencia bidireccional. Los pesos de tela más ligeros se pueden encontrar en una variedad de patrones de tejido, como sarga, satinado y mate, para diferentes propósitos.
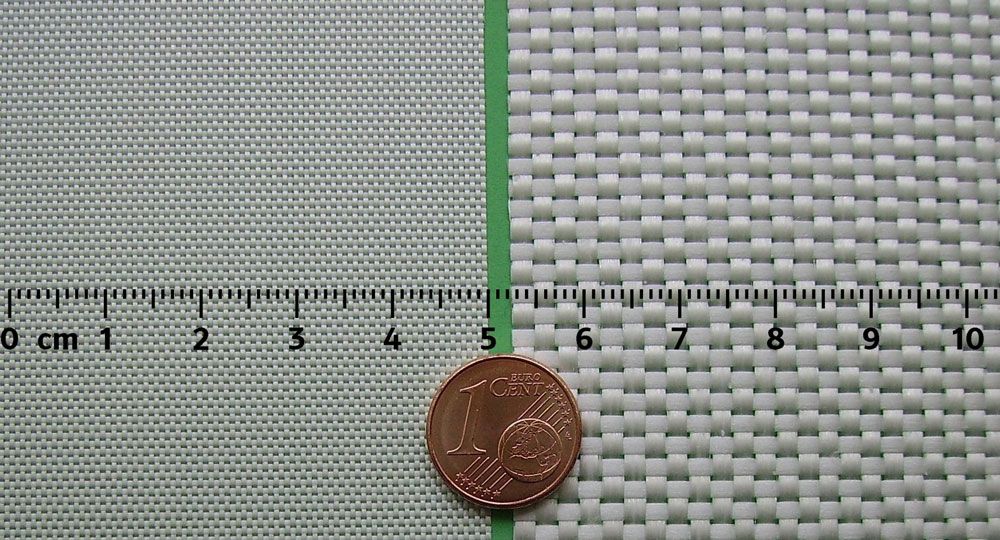
Dos ejemplos de tela de fibra de vidrio: la fibra de vidrio a la izquierda es significativamente más delgada y ligera, pero proporciona menos rigidez.
Vidrio electrónico:
Este es el paño de fibra de vidrio más utilizado en la construcción de barcos hoy en día. Puede comprar vidrio electrónico en una tienda de suministros marinos y unirlo con resina de poliéster. Está hecho de plástico fundido hilado en fibras finas que luego se tejen en tela o se juntan sueltamente para ser itinerantes.
Vidrio en S:
Este es un paño de fibra de vidrio de alto rendimiento de la industria aeronáutica. Es de tres a cinco veces más caro que el vidrio electrónico, pero también es mucho más fuerte. Desarrollado por Owens-Corning, tiene entre un 20 y un 40 por ciento más de resistencia a la tracción, al impacto y a la flexión que el vidrio electrónico. Hay dos tipos de vidrio en S: S-1, que cumple con los estándares aeroespaciales críticos y es cegadoramente caro; y S-2, que se utiliza en la industria marina. En Europa, el vidrio S se llama vidrio R.
Alfombrilla:
La alfombrilla generalmente está hecha de vidrio electrónico y consiste en fibras aleatorias de dos a tres pulgadas sostenidas en su lugar por un aglutinante soluble en resina. La estera se utiliza principalmente para el grosor y la rigidez de los edificios en capas de fibra de vidrio. La estera resiste la «impresión», donde el tejido de la mecha se muestra en la capa exterior del casco, pero también absorbe una enorme cantidad de resina y es baja en resistencia para su peso.
Fibras unidireccionales:
Este es uno de los avances en materiales de refuerzo. Consiste en hebras de fibra que corren en una sola dirección, unidas por fibras individuales que se pegan o cosen lateralmente, de la misma manera que una valla de bambú se mantiene unida por unos pocos cables. Obviamente, tiene una resistencia direccional muy alta, por lo que se puede usar en áreas donde las cargas son específicas. Debido a que no está tejido, no hay torceduras y es más fácil para los trabajadores mojarse con resina, ya que no retiene el aire como una tela de tela.
Fibras biaxiales:
Técnicamente, la mayoría de las telas son biaxiales, pero la definición moderna significa un tejido hecho de capas de tela unidireccional que no se tejen entre sí. Una capa simplemente se coloca encima de la siguiente capa para producir una banda de fibra libre de pliegues.
Fibras triaxiales:
Este es un material en capas similar a la tela biaxial, excepto que las fibras están orientadas en tres direcciones, a menudo a 120 grados entre sí para distribuir las cargas.
Materiales de Construcción avanzados de Fibra de vidrio
Fibra de carbono:
Estas fibras de grafito proporcionan una rigidez excelente, así como altas resistencias a la tracción y a la compresión, y a menudo se usan junto con vidrio en S u otros productos exóticos para proporcionar una resistencia al impacto aceptable, que de lo contrario es bastante baja. La fibra de carbono es muy cara, pero puede superar al metal en muchas situaciones. Muchas empresas producen fibra de carbono en todo el mundo y los usos dependen del contenido de carbono de la fibra en sí, algunas están destinadas a aplicaciones de alta resistencia y otras están destinadas a situaciones de alto módulo (rigidez). Es el tipo de refuerzo de fibra más caro disponible, que cuesta tanto por libra como 100 veces el vidrio electrónico común. Las fibras de carbono, superadas por el Kevlar en resistencia específica, son superiores a cualquier otra fibra en rigidez.
Kevlar:
El nombre de marca registrada de un producto DuPont, se utiliza para referirse a fibras de aramida de las que Du Pont es el único productor a nivel mundial. Un polimido aromático (generalmente acortado a aramida), el Kevlar es una forma de nailon que se desarrolló originalmente a mediados de la década de 1960 como «Fibra B» para reforzar las bandas radiales de los neumáticos. Sus propiedades únicas pronto se pusieron en otros usos, y el público generalmente piensa en Kevlar en términos de chaquetas a prueba de balas. De hecho, hay dos formas de Kevlar disponibles. El Kevlar 29 se usa para líneas, cables y chalecos antibalas, mientras que el Kevlar 49 se usa como fibra de refuerzo en compuestos de plástico. En una comparación de resistencia a peso, el Kevlar tiene la resistencia a la tracción específica más alta de cualquier fibra comercial. Es cinco veces más resistente que el acero y el doble de resistente que el vidrio electrónico, lo que permite que un casco de Kevlar mantenga la misma resistencia que un casco de vidrio electrónico a una fracción del peso. La resistencia al impacto también es un fuerte de Kevlar, y es capaz de soportar impactos repetidos, así como resistir la tendencia de otras fibras de refuerzo para permitir que las grietas se extiendan. El lado negativo del Kevlar es una marcada debilidad en la resistencia a la compresión, por lo que a menudo se usa junto con otras fibras que equilibran ese rasgo.
Nomex:
Un producto químico desarrollado por DuPont, Nomex es famoso por sus cualidades ignífugas, y se utiliza en trajes resistentes al fuego para bomberos y conductores de autos de carreras. Es una aramida, que se convierte en una sustancia similar al papel para su uso en panal.Híbridos
:
Estos son tejidos de refuerzo que combinan dos o más tipos diferentes de fibra. Un híbrido común es una mezcla de Kevlar con fibra de carbono. El kevlar proporciona una alta resistencia al impacto, mientras que la fibra de carbono proporciona la rigidez. Las combinaciones de vidrio en S, Kevlar y fibra de carbono también están disponibles para optimizar ciertas propiedades a un costo mínimo.
Materiales de núcleo avanzados
Los materiales de núcleo se utilizan a menudo para reducir el peso y aumentar la rigidez. Algunos constructores core todo el barco; otros construyen con fibra de vidrio sólida desde la línea de flotación hacia abajo y extracción de muestras por encima, y otros aún usan una mezcla de extracción de muestras y vidrio sólido en todo el barco.
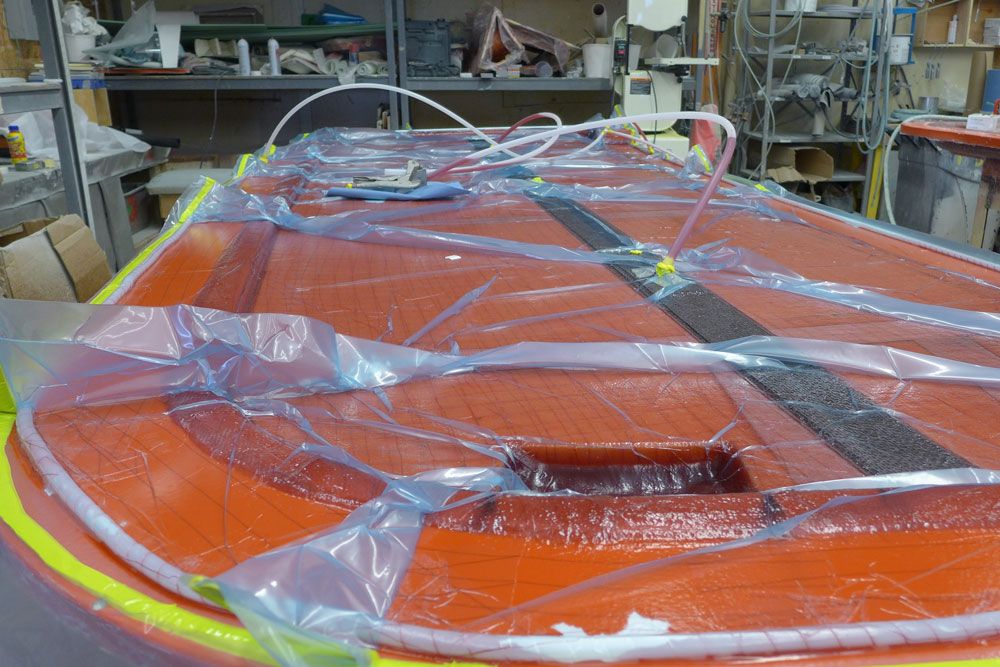
Puede ver el núcleo (con apariencia a cuadros) en esta parte, a punto de ser embolsado al vacío en Sabre Yachts. Crédito de la foto: Sabre Yachts.
Núcleo de balsa:
Cuando se usó por primera vez como refuerzo del casco, los constructores de barcos colocaron tablones largos de balsa en los cascos, pero este método llevó a la putrefacción y al fallo estructural cuando el agua «malvó» a través de toda la tabla. La balsa ha tardado mucho tiempo en sobrevivir a este comienzo, pero la balsa moderna ahora es un material de extracción de núcleos ampliamente aceptado en los barcos. La solución provino de cortar a través del grano, girarlo en el borde y producir un patrón de tablero de ajedrez de piezas de grano final que no transmiten agua. El resultado es un núcleo rígido, ligero y económico con buena calidad de impacto y alta resistencia a la compresión. Una característica adicional es la calidad de aislamiento de balsa contra el sonido, el cambio térmico y la vibración. Un factor negativo es que la balsa puede absorber la resina, lo que hace que el casco sea más pesado, pero la mano de obra de calidad puede evitar que eso suceda.
Espumas de PVC:
Airex y Klegecell (pronunciado kledge-a-cell) son los núcleos de espuma producidos comercialmente más populares que se utilizan hoy en día. Ambas son espumas de células cerradas hechas de cloruro de polivinilo, pero cada una tiene características diferentes. Airex es un PVC no reticulado, lo que lo hace más flexible y resistente a los daños. Klegecell es una espuma reticulada extremadamente rígida. Los barcos de construcción extranjera a menudo usan Divinycell, una versión escandinava de Klegecell.
Nido de abeja:
El nido de abeja es justo lo que parece: un patrón de material similar a un gofre para dar la mayor rigidez de cualquier núcleo de igual peso. Las resistencias a la compresión y al corte son insuperables, lo que podría esperarse de un material utilizado originalmente en aviones para pisos y mamparos. El nido de abeja Nomex es el que se encuentra más comúnmente en los yates, aunque definitivamente es una extravagancia de alto costo para los propietarios en busca de la última onza de ahorro de peso. Sorprendentemente, algunos panales están hechos de papel. Un papel kraft se impregna con resinas y luego se forma en un panal, lo que lo hace resistente al agua y resistente, pero el panal de papel es más pesado que Nomex. Los «paneles pelados» son láminas prefabricadas de panal que se asemejan a una pieza de madera contrachapada, y están disponibles con chapa de teca u otras capas que se pueden cortar en mamparos prefabricados de panal.Obtenga una idea de cómo funciona el núcleo dentro de una pieza de fibra de vidrio viendo nuestro video de Construcción de barcos con núcleo de espuma de Comprensión.
Técnicas avanzadas de construcción de barcos
Junto con estos nuevos materiales, los métodos para colocarlos en lo que eventualmente se convertirá en un barco también han avanzado en los últimos años. Una vez más, minimizar el peso y maximizar la resistencia es prácticamente siempre el objetivo.
Embolsado al vacío
: Este proceso comienza como una bandeja de moldeo abierta, pero el laminado húmedo está encerrado en una película de plástico y se aplica un vacío para extraer el exceso de resina. El exceso de resina no agrega resistencia, para eso es para lo que está la fibra de vidrio, pero sí agrega peso. Por lo tanto, el proceso de embolsado al vacío reduce el peso final del barco sin sacrificar la resistencia.
Infusión al vacío
: El proceso de infusión al vacío incorpora de manera similar una película de plástico y un vacío para lograr una relación ideal entre resina y vidrio. Sin embargo, en lugar de comenzar con una capa húmeda, la aspiradora, junto con un conjunto de líneas de alimentación de resina, introduce y dibuja la resina a través del paño en primer lugar. Esto permite una medición más precisa de los materiales y la capacidad de aplicar presión uniforme en un área grande, para que pueda colocar piezas más grandes.
Para obtener una explicación simplificada de cómo funciona el proceso de vacío al moldear embarcaciones, vea nuestro video Comprender el embolsado al vacío.
Métodos alternativos de construcción de embarcaciones
Mientras que la gran mayoría de los barcos recreativos construidos hoy en día dependen de estos materiales y métodos, hay excepciones. La mayoría de las veces los encontrará con yates grandes, donde el precio no es un problema. Algunos todavía están construidos con cascos de metal, y otros con técnicas como «moldeo en frío» o «tablón en el marco».»En estos casos, la estructura del barco está hecha de madera que luego se superpone o encapsula en fibra de vidrio y resina epoxi colocadas a mano. Yates de pesca deportiva como un convertible de 73 pies Bayliss, y cruceros de alta gama como los yates Vicem, se construyen con estos métodos.
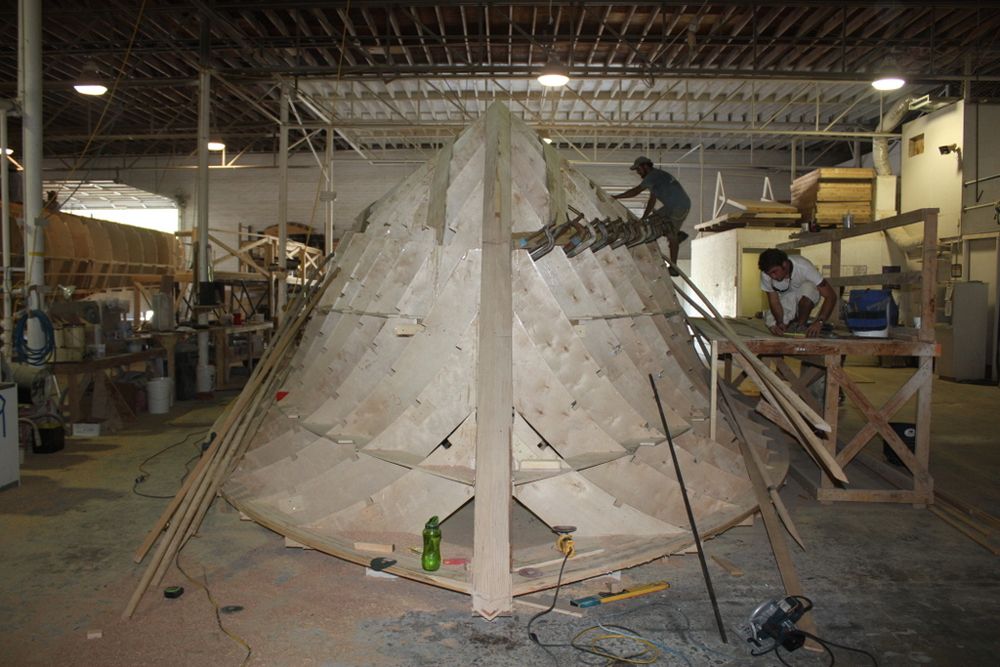
Aunque muchos constructores de barcos modernos evitan el uso de madera, en yates personalizados de alta gama como este Jarrett Bay, los métodos como el moldeado en frío a menudo se consideran superiores a las técnicas más modernas.
En el extremo opuesto del extremo, tienes barcos FRP sin la F o la R y solo el plástico P. Aunque los barcos de plástico más grandes en producción tienen menos de 20 pies de longitud (y la mayoría tienen menos de 12 o 14 pies), el plástico moldeado roto se ha vuelto muy popular en los mercados de kayak y botes. Estas embarcaciones simples y económicas están formadas por gránulos de plástico que se funden dentro de un horno giratorio, que también es un molde. Cuando se enfría, el plástico ha tomado la forma del molde y sale un bote.
Ahora que conoce los conceptos básicos de la construcción de barcos modernos y está listo para elegir un barco por su cuenta, asegúrese de leer Cómo comprar un barco: Consejos para compradores por primera vez.Nota del editor: Este artículo incorpora partes de un artículo Básico de Construcción de barcos de Chris Caswell, de agosto de 2000, y se actualizó en octubre de 2018 y marzo de 2020.