Bootsbau: Grundkonstruktion aus Harz, Glasfaser und Kernen
Viele Menschen fragen sich, wie moderne Glasfaserboote gebaut werden, und der Bootsbau ist heute überhaupt nicht mehr so wie damals, als antike und klassische Motorboote gebaut wurden. Heutzutage ist Bootsbau eigentlich ziemlich High-Tech.
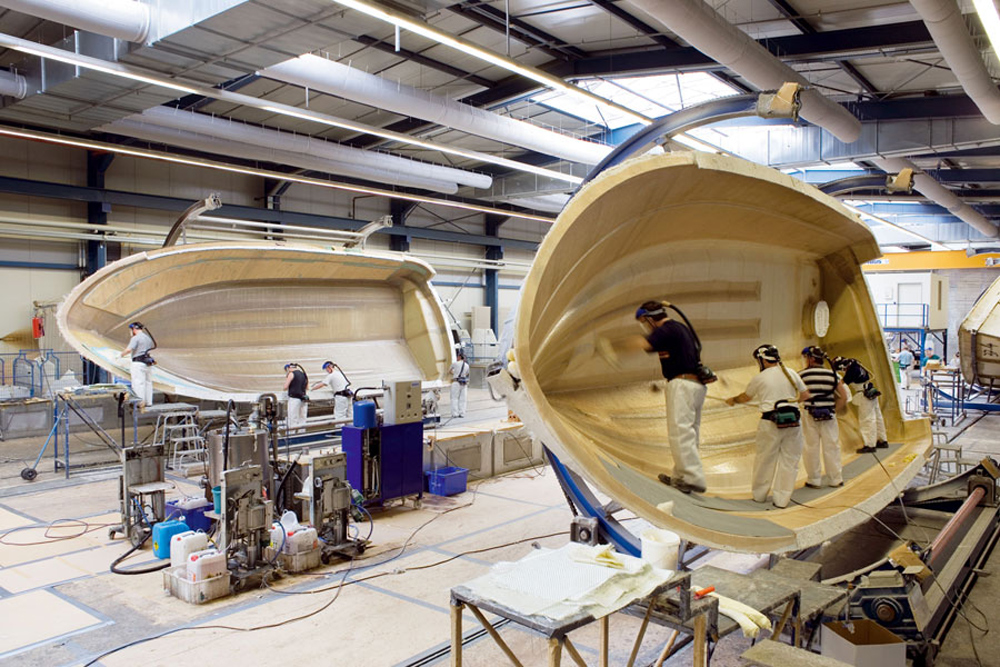
In der Neuzeit beginnt der Bau eines Bootes mit einer Form. Diese werden verwendet, um Bavaria Powerboats zu erstellen.
Grundlagen des Bootsbaus
Vor der Entwicklung von Glasfaserbautechniken wurden Boote aus Holz, Stahl und anderen Materialien gebaut, indem Teile und Teile zu einer Struktur zusammengebaut wurden, die dann mit einem Rumpf ummantelt wurde. Beim Bau von Glasfaserbooten werden jedoch die Hauptkomponenten des Bootes – Rumpf, Deck, Liner und große Teile wie Konsolen — aus Glasfaser geformt. Normalerweise bedeutet dies, mit einer weiblichen Form zu beginnen. Die Form wird zuerst mit Gelcoat besprüht, dann wird ein Glasfasertuch aufgetragen und dann wird Harz verwendet, um das Fiberglas zu sättigen oder zu „benetzen“. Wenn das Harz aushärtet, haben Sie einen Rumpf oder ein Bootsteil (eine Erklärung der verschiedenen Bootsteile finden Sie in unserem Anfängerleitfaden zur Bootsterminologie).
Strukturelle Verstärkungen wie Stringer und Schotte können separat geformt und dann mit Glasfaser auf das Teil aufgebracht oder in einigen Fällen gleichzeitig verlegt werden. Während der Rumpf noch offen und freigelegt ist, können Gegenstände, die sich unter Deck befinden, wie Kraftstoff- und Wassertanks oder Innenbordmotoren, montiert werden. Dies ist auch der Fall, wenn Rohrleitungen und Verkabelungen ausgeführt werden können. Dann werden die Hauptkomponenten zusammengebaut. Bei den meisten modernen Motorbooten bedeutet dies, dass das Deck und / oder der Liner oft mit einem Kran angehoben und in den Rumpf abgesenkt werden.
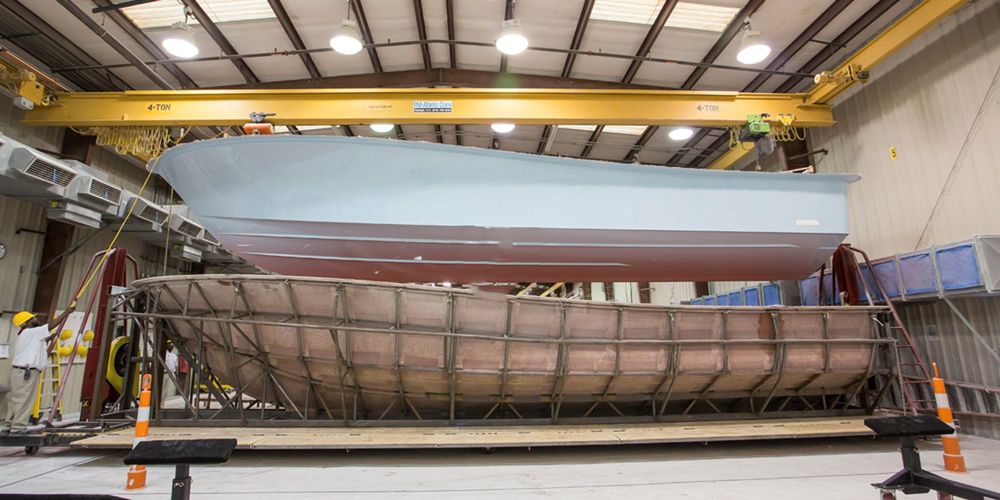
Brückenkräne werden häufig verwendet, um wichtige Bootsteile, wie diesen Rumpf für ein Regulator-Fischerboot, aus den Formen in Position für die weitere Montage zu heben.
Viele Boote sind mit einer „Schuhkarton“ -Verbindung konstruiert, bei der Rumpf und Deck Gegenflansche haben oder sich überlappen. Oft werden mechanische Befestigungselemente wie Schrauben oder Durchgangsbolzen verwendet, um die Teile zusammen zu befestigen, zusätzlich zur Verwendung eines chemischen Bindemittels und Dichtmittels wie Methylmethacrylat oder 3M 5200, wodurch die Verbindung auch wasserdicht wird. Zusätzlich, einige Bauherren Fiberglas um den Umfang des Rumpfes an Deck Gelenk.
Nachdem die wichtigsten Teile des Bootes zusammengebaut sind, können Innenausstattungen wie Sitze und Lenkräder hinzugefügt werden. Schließlich können die Details und der letzte Schliff erledigt werden.
Änderungen beim Bau eines Bootes
Die erste Revolution im modernen Bootsbau war offensichtlich die Verlagerung von hauptsächlich Holz- zu hauptsächlich Glasfaserkonstruktion, aber eine zweite war viel subtiler. Es gab einen Übergang von herkömmlichen Glasfasermethoden zu einer Vielzahl exotischer Materialien und Techniken, die selbst den erfahrenen Segler mit Schlagworten und Jargon verwirren können.
Das Konzept bleibt jedoch im Wesentlichen gleich. Fiberglas (richtig genannt glasfaserverstärkter Kunststoff oder FRP) ist immer noch ein Fasermaterial, das in eine Bindesubstanz aus Harz eingebettet ist. In den frühen Jahren war Glasfaser buchstäblich Glasfasern, aber das änderte sich bald zu Fasern aus verschiedenen synthetischen Kunststoffen. Seit vielen Jahren besteht eine Glasfaserkonstruktion aus Stoff, Roving, Matte und Harzen, die Sie in jedem Baumarkt kaufen können. In jüngerer Zeit kam es zu fortschrittlicheren Materialien wie Kevlar und Kohlefaser, die viele Menschen aus ihrer Verwendung in anderen Produkten kennen. Heutzutage werden jedoch so viele verschiedene Materialien verwendet, dass ein Abschluss in Chemieingenieurwesen hilfreich ist, wenn Sie die Broschüre für ein neues Boot lesen.Einige der Fortschritte kamen von den Bemühungen der Erbauer von Offshore-Rennmotorbooten und Ocean Racing Segelbooten, leichtere, stärkere und damit schnellere Boote zu produzieren, aber die wirklichen Auswirkungen kamen mit der Energiekrise. Da Glasfaser ein petrochemisches Produkt ist, war es für Bootsbauer sinnvoll, nach Möglichkeiten zu suchen, Boote ohne Festigkeitsverlust leichter zu machen, da jedes Pfund Glasfaser dem Bauherrn Geld gespart hat. Für Motorbootbauer ist ein leichtes, aber starkes Boot auch kraftstoffeffizienter.
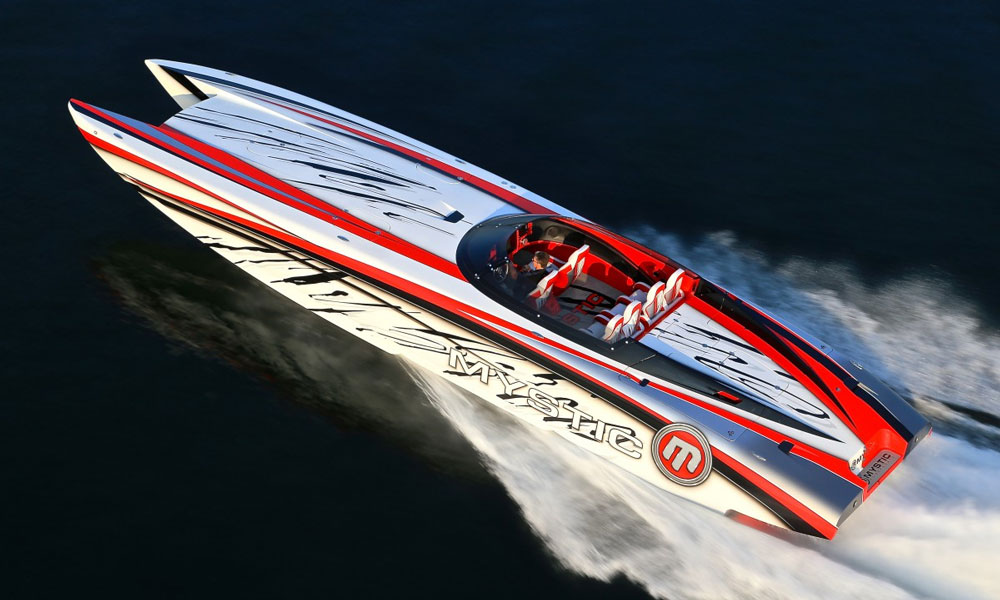
Die Entwicklung ernsthafter Schnellboote wie dieses Mystic-Katamarans spielte eine bedeutende Rolle, da die Hersteller lernten, wie man das Gewicht minimiert. Es waren jedoch die Baukosten, die diesen Trend bei Bootsbauern aller Art beflügelten.
Ein Großteil der Forschung und Entwicklung kam tatsächlich aus der Flugzeug- und Luftfahrtindustrie, wo Festigkeit und geringes Gewicht schon immer Hauptanliegen waren, und das Rinnsal der Technologie ist zu einem solchen Wasserfall geworden, dass viele Bootsbesitzer sind sich der Veränderungen sowohl bei neuen Materialien als auch bei neuen Formtechniken nicht bewusst.
Arten von Glasfaserharz
Es gibt drei Arten von Harzen: Polyester, Vinylester und Epoxid. Jeder hat seinen Platz in der Welt des Bootsbaus. Der wichtige Faktor ist, damit der Erbauer das Harz zur Art des Verstärkungsmaterials richtig zusammenbringt, das benutzt wird, damit die Stärken zusammengebracht werden. Zum Beispiel ist ein Vinylesterharz ideal für S-Glas, aber wenn es mit E-Glas verwendet wird, wird das Verstärkungsmaterial vor dem Harz versagen.
Polyester:
Dies ist das Harz, das heute am häufigsten für den Bootsbau verwendet wird, und die meisten Bootsbesitzer sind damit vertraut. Es ist kostengünstig und in der Regel universell einsetzbar. Es hat geringe Dehnungseigenschaften (Dehnung), so dass es nicht auf modernen Hochleistungsbooten verwendet wird, aber es ist für die meisten Boote vollkommen ausreichend. Der allgemeinste Polyester ist eine orthophthalische Basis, aber neuere isophthalische ansässige Polyester gewinnen in der Popularität. Die Isophthalics sind gegen Wasser und Chemikalien beständiger, sind abnutzungsbeständiger und haben höhere Auswirkung und Ermüdungsleistung (Flex). Die meisten modernen Gelcoat-Oberflächen werden mit Isophthalharzen hergestellt.
Vinylester:
Eine alternative zu polyester, vinylester haben bessere stretch eigenschaften als polyester, so sie mehr eng spiel die stärken der verschiedenen exotischen verstärkungen. Vinylester hat auch eine gute Wasserbeständigkeit und Ermüdungseigenschaften, aber es ist teurer als Polyesterharz. Ein wichtiges Merkmal von Vinylester ist, dass es eine ausgezeichnete sekundäre Haftfestigkeit aufweist, so dass Schotte oder Stringer, die einem gehärteten Rumpf hinzugefügt werden, eine bessere Bindung aufweisen als auf einem Polyesterrumpf.
Epoxy:
Dies ist ein Hochleistungsharz mit einem passenden Preisschild. Epoxidharze haben den Ruf, schwer zu bearbeiten zu sein, da frühe Epoxide dick waren, aber viele moderne Epoxide sind ziemlich flüssig. Epoxy haftet besser als jedes andere Harz auf einer Vielzahl von Materialien, was es ideal zum Anbringen von Kernen, Stringern oder anderen Gegenständen macht.
Arten von Glasfasergewebe
Gewebe mit kontinuierlichen Strängen sind die häufigsten Tücher mit Gewichten von vier bis 15 Unzen pro Quadratmeter. Schwerere Gewichte, die normalerweise als Roving oder gewebtes Roving bezeichnet werden, bestehen aus unverdrillten Fasergarnen mit einem Gewicht von bis zu 48 Unzen pro Yard. Das fertige Roving ähnelt einem groben Sackleinen und hat wie alle Tücher eine gute bidirektionale Festigkeit. Die leichteren Stoffgewichte können in einer Vielzahl von Webmustern, wie Köper, Satin und matt, für verschiedene Zwecke gefunden werden.
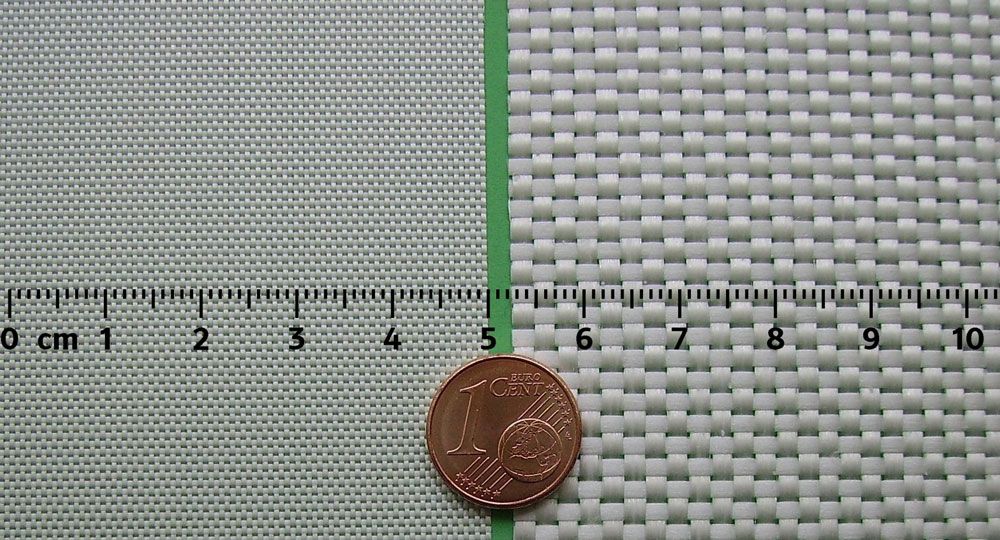
Zwei Beispiele für Glasfasergewebe: Das Glasfasergewebe links ist deutlich dünner und leichter, bietet jedoch weniger Steifigkeit.
E-Glas:
Dies ist heute das am häufigsten verwendete Glasfasergewebe im Bootsbau. Sie können E-Glas in einem Schifffahrtsgeschäft kaufen und mit Polyesterharz verkleben. Es wird aus geschmolzenem Kunststoff hergestellt, der zu feinen Fasern gesponnen wird, die dann entweder zu Stoff gewebt oder lose zu Roving gesammelt werden.
S-Glas:
Dies ist ein Hochleistungs-Glasfasergewebe aus der Flugzeugindustrie. Es ist drei- bis fünfmal teurer als E-Glas, aber es ist auch viel stärker. Entwickelt von Owens-Corning, hat es 20 bis 40 Prozent höhere Zug-, Schlag- und Biegefestigkeit als E-Glas. Es gibt zwei Arten von S-Glas: S-1, das kritische Luftfahrtstandards erfüllt und blendend teuer ist; und S-2, das in der Schifffahrtsindustrie verwendet wird. In Europa wird S-Glas als R-Glas bezeichnet.
Mat:
Mat besteht normalerweise aus E-Glas und besteht aus zufälligen Zwei- bis Drei-Zoll-Fasern, die von einem harzlöslichen Bindemittel gehalten werden. Matte wird hauptsächlich für den Aufbau von Dicke und Steifigkeit in Glasfaser-Layups verwendet. Matte widersteht „Print-Through“, wo das Gewebe von Roving in der äußeren Schicht des Rumpfes zeigt, aber es saugt auch eine enorme Menge an Harz auf und ist in der Stärke für sein Gewicht niedrig.
Unidirektionale Fasern:
Dies ist einer der Fortschritte bei Verstärkungsmaterialien. Es besteht aus Fasersträngen, die nur in eine Richtung verlaufen und von einzelnen Fasern zusammengehalten werden, die seitlich geklebt oder genäht werden, ähnlich wie ein Bambuszaun von einigen Drähten zusammengehalten wird. Offensichtlich hat es eine sehr hohe Richtfestigkeit, so dass es in Bereichen verwendet werden kann, in denen die Lasten spezifisch sind. Da es nicht gewebt ist, gibt es keine Knicke und es ist einfacher für Arbeiter, mit Harz zu benetzen, da es keine Luft wie ein Stoff hält.
Biaxiale Fasern:
Technisch gesehen sind die meisten Stoffe biaxial, aber die moderne Definition bedeutet einen Stoff, der aus unidirektionalen Stoffschichten besteht, die nicht durcheinandergewebt sind. Eine Schicht legt einfach auf die nächste Schicht, um ein knickfreies Faserband zu erzeugen.
Triaxiale Fasern:
Dies ist ein Schichtmaterial, das einem biaxialen Tuch ähnelt, mit der Ausnahme, dass die Fasern in drei Richtungen ausgerichtet sind, häufig um 120 Grad zueinander, um die Lasten zu verteilen.
Erweiterte Fiberglas Bau Materialien
Carbon Faser:
Diese Graphitfasern bieten eine hervorragende Steifigkeit sowie hohe Zug- und Druckfestigkeiten und werden häufig in Verbindung mit S-Glas oder anderen Exoten verwendet, um eine akzeptable Schlagfestigkeit zu erzielen, die ansonsten recht gering ist. Kohlefaser ist sehr teuer, kann aber in vielen Situationen Metall übertreffen. Viele Firmen produzieren Kohlenstofffaser weltweit und die Verwendungen hängen vom Kohlenstoffgehalt der Faser selbst ab, wobei einige für hochfeste Anwendungen bestimmt sind und andere für Situationen mit hohem Modul (Steifigkeit). Es ist die teuerste verfügbare Art der Faserverstärkung und kostet so viel pro Pfund wie das 100-fache des üblichen E-Glases. An zweiter Stelle nach Kevlar in Bezug auf die spezifische Festigkeit sind Kohlenstofffasern jeder anderen Faser in Bezug auf die Steifigkeit überlegen.
Kevlar:
Der geschützte Name für ein DuPont-Produkt bezieht sich auf Aramidfasern, von denen Du Pont der einzige Produzent weltweit ist. Kevlar ist ein aromatisches Polymid (normalerweise verkürzt auf Aramid) und eine Form von Nylon, das ursprünglich Mitte der 1960er Jahre als „Faser B“ zur Verstärkung von Radialreifengurten entwickelt wurde. Seine einzigartigen Eigenschaften wurden bald in andere Verwendungen gebracht, und die Öffentlichkeit denkt normalerweise an Kevlar in Bezug auf kugelsichere Jacken. Es gibt tatsächlich zwei Formen von Kevlar. Kevlar 29 wird für Leitungen, Kabel und Flakmäntel verwendet, während Kevlar 49 als Verstärkungsfaser in Kunststoffverbundwerkstoffen verwendet wird. Im Vergleich von Festigkeit zu Gewicht hat Kevlar die höchste spezifische Zugfestigkeit aller handelsüblichen Fasern. Es ist fünfmal stärker als Stahl und doppelt so stark wie E-Glas, wodurch ein Kevlar-Rumpf die gleiche Festigkeit wie ein E-Glas-Rumpf bei einem Bruchteil des Gewichts beibehalten kann. Schlagfestigkeit ist auch eine Kevlar-Stärke, und es ist in der Lage, wiederholten Stößen standzuhalten und der Tendenz anderer Verstärkungsfasern zu widerstehen, Risse ausbreiten zu lassen. Die negative Seite zu Kevlar ist eine markierte Schwäche in der Kompressionsstärke, also wird sie häufig in Verbindung mit anderen Fasern verwendet, die dieses Merkmal balancieren.
Nomex:
Nomex, eine von DuPont entwickelte Chemikalie, ist vor allem für ihre feuerfesten Eigenschaften bekannt und wird in feuerfesten Anzügen für Feuerwehrleute und Rennfahrer verwendet. Es ist ein Aramid, das in eine papierähnliche Substanz zur Verwendung in Waben umgewandelt wird.
Hybriden:
Dies sind Verstärkungsgewebe, die zwei oder mehr verschiedene Fasertypen kombinieren. Ein üblicher Hybrid ist eine Mischung aus Kevlar und Kohlefaser. Das Kevlar bietet eine hohe Schlagfestigkeit, während die Kohlefaser die Steifigkeit liefert. Kombinationen aus S-Glas, Kevlar und Kohlefaser sind ebenfalls erhältlich, um bestimmte Eigenschaften zu minimalen Kosten zu optimieren.
Fortschrittliche Kernmaterialien
Kernmaterialien werden häufig verwendet, um das Gewicht zu reduzieren und die Steifigkeit zu erhöhen. Einige Bauherren entkernen das gesamte Boot; andere konstruieren mit massivem Fiberglas von der Wasserlinie nach unten und Entkernen oben, und wieder andere verwenden eine Mischung aus Entkernen und massivem Glas im gesamten Boot.
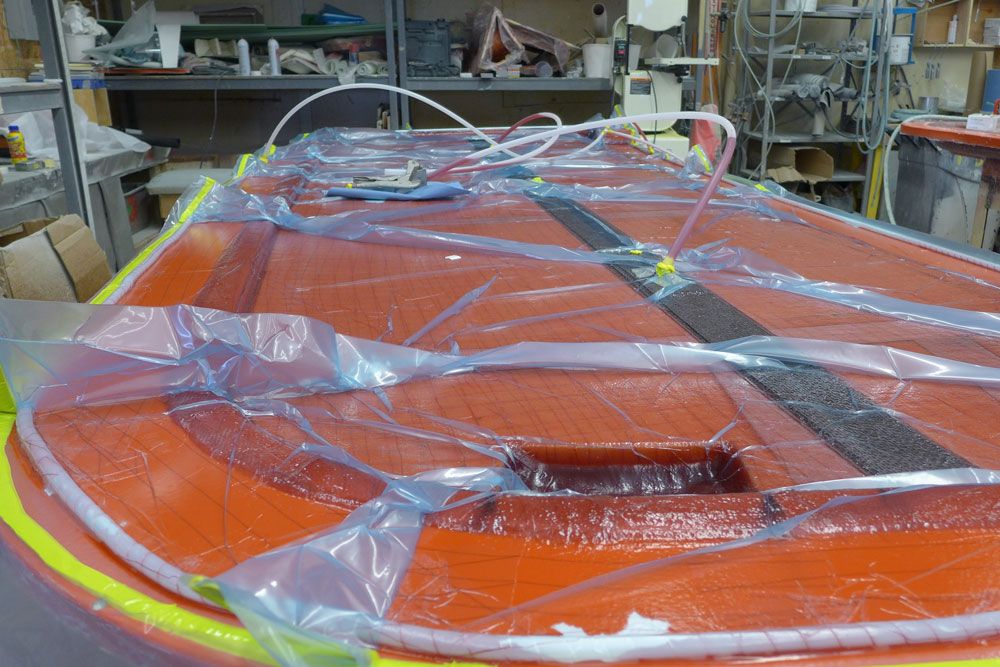
In diesem Teil sehen Sie den Kern (mit kariertem Aussehen), der bei Sabre Yachts im Vakuum verpackt werden soll. Bildnachweis: Sabre Yachts.
Balsa-Kern:
Bei der ersten Verwendung als Rumpfversteifung legten Bootsbauer lange Balsa-Bretter in die Rümpfe, aber diese Methode führte zu Fäulnis und strukturellem Versagen, wenn Wasser durch die gesamte Planke „floss“. Es hat lange gedauert, bis Balsa diesen Anfang durchgemacht hat, aber modernes Balsa ist heute ein weithin akzeptiertes Kernmaterial in Booten. Die Lösung bestand darin, das Korn zu durchschneiden, es auf die Kante zu drehen und ein Schachbrettmuster aus Endkornstücken zu erzeugen, die kein Wasser durchlassen. Das Ergebnis ist ein steifer, leichter und kostengünstiger Kern mit guter Schlagzähigkeit und hoher Druckfestigkeit. Ein zusätzliches Merkmal ist die Isolationsqualität von Balsa gegen Schall, thermische Veränderungen und Vibrationen. Ein negativer Faktor ist, dass Balsa Harz absorbieren kann, wodurch der Rumpf schwerer wird, aber eine hochwertige Verarbeitung kann dies verhindern.
PVC-Schäume:
Airex und Klegecell (ausgesprochen kledge-a-cell) sind die beliebtesten kommerziell hergestellten Schaumkerne, die heute verwendet werden. Beide sind geschlossenzellige Schäume aus Polyvinylchlorid, aber jeder hat unterschiedliche Eigenschaften. Airex ist ein nicht vernetztes PVC, wodurch es flexibler und widerstandsfähiger gegen Beschädigungen ist. Klegecell ist ein vernetzter Schaumstoff, der extrem steif ist. Im Ausland gebaute Boote verwenden häufig Divinycell, eine skandinavische Version von Klegecell.
Honeycomb:
Honeycomb ist genau das, wonach es sich anhört: ein waffelartiges Materialmuster, das die höchste Steifigkeit eines Kerns mit gleichem Gewicht bietet. Die Druck- und Scherfestigkeiten sind unübertroffen, was von einem Material erwartet werden könnte, das ursprünglich in Flugzeugen für Bodenbeläge und Schotte verwendet wurde. Nomex Honeycomb ist am häufigsten auf Yachten zu finden, obwohl es definitiv eine Extravaganz für Besitzer ist, die auf der Suche nach der letzten Unze Gewichtseinsparung sind. Überraschenderweise bestehen einige Waben aus Papier. Ein Kraftpapier wird mit Harzen imprägniert und dann zu einer Wabe geformt, wodurch es sowohl wasserdicht als auch robust ist, aber die Papierwabe ist schwerer als Nomex. „Gehäutete Paneele“ sind vorgefertigte Wabenblätter, die einem Stück Sperrholz ähneln, und sind mit Teakholzfurnier oder verschiedenen anderen Überlagerungen erhältlich, die in vorgefertigte Wabenschotte geschnitten werden können.
Erhalten Sie einen Einblick in die Funktionsweise des Kerns in einem Glasfaserteil, indem Sie sich unser Video zum Bau von Schaumstoffbooten ansehen.
Fortgeschrittene Bootsbautechniken
Zusammen mit diesen neuen Materialien haben sich in den letzten Jahren auch Methoden entwickelt, um sie zu einem Boot zu machen. Auch hier ist die Minimierung des Gewichts bei gleichzeitiger Maximierung der Festigkeit praktisch immer das Ziel.
Vakuumverpackung
: Dieser Prozess beginnt wie ein offener Formteilaufbau, aber das nasse Laminat wird in eine Kunststofffolie eingeschlossen und ein Vakuum angelegt, um überschüssiges Harz herauszuziehen. Überschüssiges Harz erhöht nicht die Festigkeit – dafür ist das Fiberglas da -, aber es erhöht das Gewicht. Der Vakuum-Absackprozess reduziert also das Gewicht des Bootes, ohne auf Festigkeit zu verzichten.
Vakuuminfusion
: Der Vakuuminfusionsprozess beinhaltet ebenfalls Kunststofffolie und ein Vakuum, um ein ideales Harz-Glas-Verhältnis zu erreichen. Anstatt jedoch mit einem nassen Auflegen zu beginnen, führt das Vakuum zusammen mit einer Reihe von Harzzuführleitungen das Harz zunächst durch das Tuch ein und zieht es an. Dies ermöglicht eine präzisere Messung der Materialien und die Möglichkeit, einen gleichmäßigen Druck über eine große Fläche auszuüben, sodass Sie größere Teile auflegen können.Für eine vereinfachte Erklärung, wie der Vakuumprozess beim Formen von Booten funktioniert, sehen Sie sich unser Understanding Vacuum Bagging Video an.
Alternative Bootsbaumethoden
Während die überwiegende Mehrheit der heute gebauten Freizeitboote auf diesen Materialien und Methoden beruht, gibt es Ausnahmen. Meistens findet man sie bei großen Yachten, bei denen der Preis keine Rolle spielt. Einige sind immer noch mit Metallrümpfen gebaut, und einige andere mit Techniken wie „Kaltformen,“Oder „Planke auf Rahmen.“ In diesen Fällen wird die Struktur des Bootes aus Holz gefertigt, das dann mit handverlegtem Fiberglas und Epoxidharz geschichtet oder eingekapselt wird. Sportfischeryachten wie ein Bayliss 73 Fuß Cabrio und High-End-Kreuzer wie Vicem Yachts werden mit diesen Methoden gebaut.
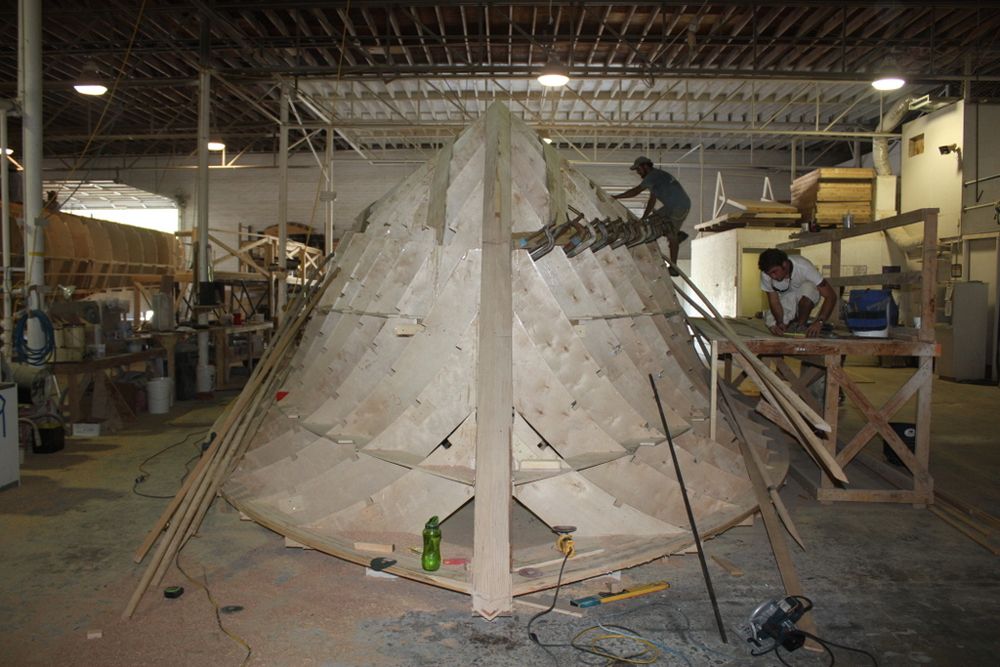
Obwohl viele moderne Bootsbauer die Verwendung von Holz meiden, werden bei High-End-Custom-Yachten wie dieser Jarrett Bay Methoden wie das Kaltformen oft als modernen Techniken überlegen angesehen.
Am entgegengesetzten Ende des Extrems haben Sie GFK-Boote ohne F oder R und nur den P – Kunststoff. Obwohl die größten Vollkunststoffboote in der Produktion unter 20 Fuß lang sind (und die meisten unter 12 oder 14 Fuß), ist rotationsgeformter Kunststoff auf dem Kajak- und Beibootmarkt sehr beliebt geworden. Diese einfachen, kostengünstigen Formen werden aus Kunststoffpellets gebildet, die in einem rotierenden Ofen, der auch eine Form ist, eingeschmolzen werden. Wenn es abkühlt, hat der Kunststoff die Form der Form angenommen und ein Boot springt heraus.Jetzt, da Sie die Grundlagen des modernen Bootsbaus kennen und bereit sind, ein eigenes Boot zu wählen, lesen Sie unbedingt Wie man ein Boot kauft: Tipps für Erstkäufer.Anmerkung des Herausgebers: Dieser Artikel enthält Teile eines grundlegenden Bootsbauartikels von Chris Caswell aus dem August 2000 und wurde im Oktober 2018 und März 2020 aktualisiert.