Boat Building: Basic Construction of hars, Fiberglass, and Cores
veel mensen vragen zich af hoe moderne fiberglass boten worden gebouwd, en boat building vandaag de dag is helemaal niet zoals het was toen antieke en klassieke motorboten werden gebouwd. Tegenwoordig is bootbouw behoorlijk hightech.
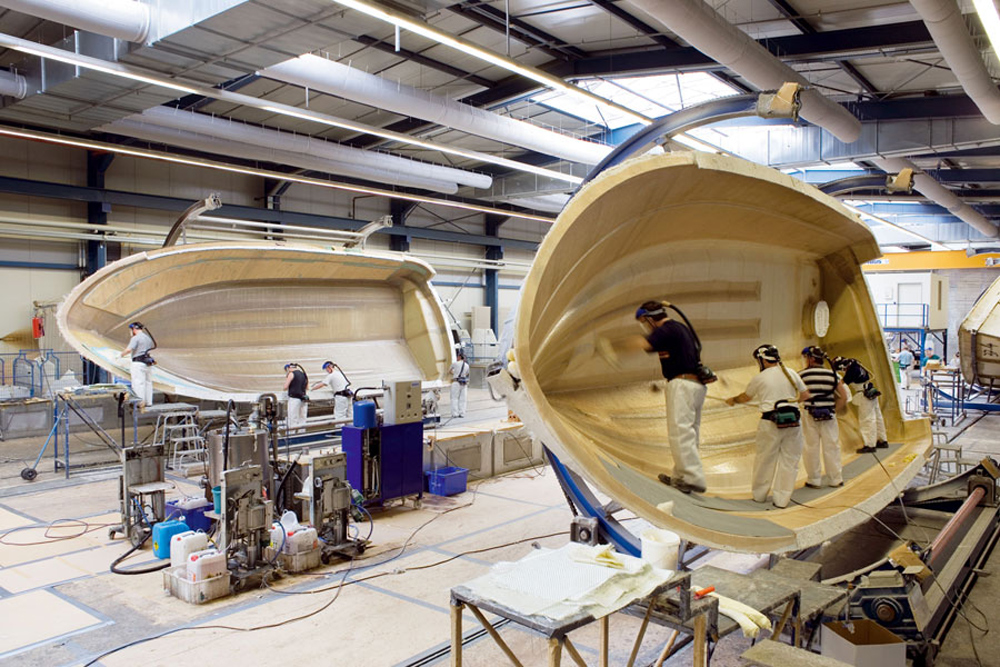
in de moderne tijd begint het bouwen van een boot met een mal. Deze zullen worden gebruikt om Bavaria motorboten te maken.
basis voor het bouwen van boten
vóór de ontwikkeling van glasvezel bouwtechnieken werden boten gebouwd van hout, staal en andere materialen, door stukken en onderdelen samen te voegen tot een structuur die vervolgens werd omhuld met een romp. Met glasvezel boot gebouw, echter, de belangrijkste onderdelen van de boot – de romp, dek, voering, en grote delen zoals consoles—zijn gegoten uit glasvezel. Meestal betekent dit te beginnen met een vrouwelijke schimmel. De mal wordt eerst gespoten met gelcoat, vervolgens wordt glasvezel doek aangebracht en vervolgens wordt hars gebruikt om de glasvezel te verzadigen of “nat te maken”. Wanneer de hars uithardt, heb je een romp of een bootdeel (voor een uitleg van de verschillende bootonderdelen, zie onze Beginnersgids voor Bootterminologie).structurele versterkingen zoals stringers en schotten kunnen afzonderlijk worden gegoten en vervolgens met glasvezel op het onderdeel worden aangebracht, of kunnen in sommige gevallen tegelijkertijd worden gelegd. Terwijl de romp nog open en bloot, items die zal worden geplaatst benedendeks niveau zoals brandstof en watertanks of binnenboordmotoren kunnen worden gemonteerd. Dit is ook wanneer sanitair en bedrading kan worden uitgevoerd. Vervolgens worden de belangrijkste componenten geassembleerd. Voor de meeste moderne motorboten betekent dit dat het dek en/of de voering wordt opgetild, vaak met een kraan, en in de romp wordt neergelaten.
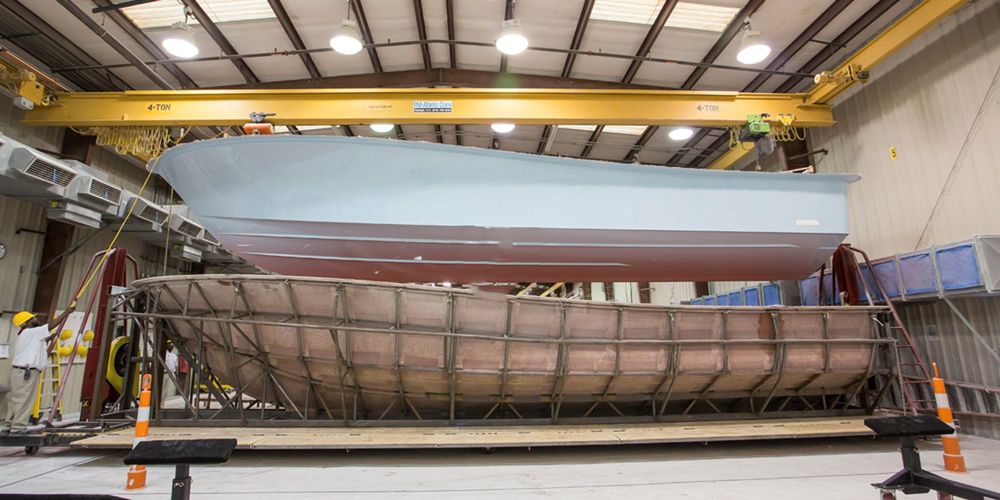
Bovenloopkranen worden vaak gebruikt om belangrijke bootonderdelen, zoals deze romp voor een regulerende vissersboot, uit de mallen te tillen en in positie te brengen voor verdere montage.
veel boten zijn ontworpen met een” schoenendoos ” -verbinding waarbij de romp en het dek elkaar overlappen. Vaak worden mechanische bevestigingsmiddelen zoals schroeven of door-bouten gebruikt om de onderdelen aan elkaar te bevestigen, naast het gebruik van een chemisch bindmiddel en afdichtmiddel zoals methylmethacrylaat of 3M 5200, die ook de verbinding waterdicht maakt. Bovendien, sommige bouwers glasvezel rond de omtrek van de romp aan dek gezamenlijke.
Met de belangrijkste onderdelen van de boot geassembleerd, interieur zoals stoelen en stuurwielen kan dan worden toegevoegd. Tot slot kunnen de details en afwerking worden verzorgd.
veranderingen in het bouwen van een boot
De eerste revolutie in de moderne scheepsbouw was duidelijk de verschuiving van voornamelijk hout naar voornamelijk glasvezel constructie, maar een tweede was veel subtieler. Er is een overgang geweest van conventionele glasvezel methoden om een groot aantal exotische materialen en technieken die zelfs de ervaren zeiler kan verwarren met modewoorden en jargon.het concept blijft echter in wezen hetzelfde. Glasvezel (goed genoemd glasvezel versterkte kunststof, of FRP) is nog steeds een vezelmateriaal in een bindende stof van hars. In de zeer vroege jaren, glasvezel was letterlijk vezels van glas, maar dat al snel veranderd in vezels van verschillende synthetische kunststoffen. Al vele jaren is een glasvezel constructie van doek, zwerven, mat, en harsen die u kunt kopen in elke ijzerhandel. Meer recent kwam het om meer geavanceerde materialen zoals Kevlar en koolstofvezel, die veel mensen bekend zijn met van hun gebruik in andere producten. Tegenwoordig worden er echter zoveel verschillende materialen gebruikt dat een diploma in chemische techniek nuttig is bij het lezen van de brochure voor een nieuwe boot.een deel van de vooruitgang kwam van de inspanningen van de bouwers van offshore racing motorboten en ocean racing zeilboten om lichtere, sterkere en dus snellere boten te produceren, maar de echte impact kwam met de energiecrisis. Aangezien glasvezel een petrochemisch product is, was het zinvol voor bootbouwers om manieren te onderzoeken om Boten lichter te maken zonder verlies van kracht, omdat elk pond glasvezel geëlimineerd de bouwer geld bespaart. Voor motorbootbouwers is een lichte maar sterke boot ook zuiniger.
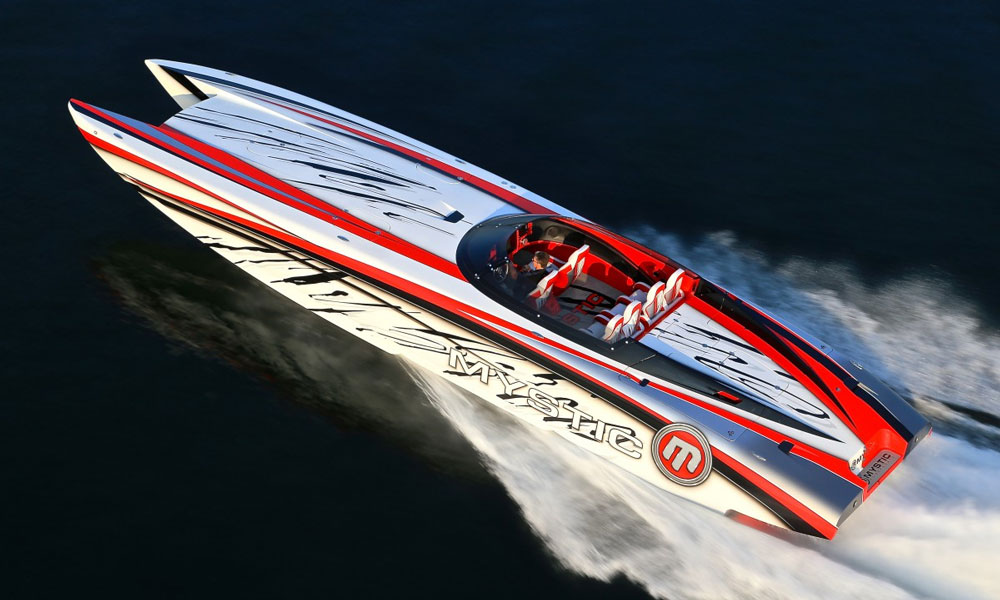
de ontwikkeling van serieuze speedboten, zoals deze mystieke catamaran, speelde een belangrijke rol toen fabrikanten leerden gewicht te minimaliseren. Het waren de kosten van de bouw, echter, die deze trend onder boot-bouwers van alle soorten gestimuleerd.een groot deel van het onderzoek en de ontwikkeling kwam eigenlijk uit de vliegtuig-en lucht-en ruimtevaartindustrie, waar kracht en lichtgewicht altijd de belangrijkste zorg waren, en het doorsijpelen van technologie is zo ‘ n waterval geworden dat veel booteigenaren zich niet bewust zijn van de veranderingen die plaatsvinden in zowel nieuwe materialen als nieuwe vormtechnieken.
soorten Glasvezelhars
er zijn drie soorten harsen: polyester, vinylester en epoxy. Elk heeft een plaats in de boot-bouwwereld. De belangrijke factor is dat de bouwer de hars correct aanpast aan het type versterkingsmateriaal dat wordt gebruikt, zodat de sterktes worden afgestemd. Een vinylesterhars is bijvoorbeeld ideaal voor S-glas, maar bij gebruik met E-glas zal het versterkingsmateriaal voor de hars falen.
Polyester:
Dit is de hars die tegenwoordig het meest wordt gebruikt voor de scheepsbouw, en de meeste booteigenaren zijn ermee bekend. Het is goedkoop en over het algemeen alle-doel. Het heeft lage rek (rek) eigenschappen dus het wordt niet gebruikt op moderne high-performance boten, maar het is perfect geschikt voor de meeste boten. De meest voorkomende polyester is een orthoftalische basis, maar nieuwere isoftalische basis polyesters winnen aan populariteit. De isoftalica zijn beter bestand tegen water en chemicaliën, zijn meer slijtvast, en hebben een hogere impact en vermoeidheid (flex) prestaties. De meeste moderne gelcoatafwerkingen zijn gemaakt met isoftaalharsen.
Vinylester:vinylesters, een alternatief voor polyester, hebben betere rekeigenschappen dan polyesters, zodat ze beter overeenkomen met de sterkte van de verschillende exotische versterkingen. Vinylester heeft ook goede waterbestendigheid en vermoeidheidseigenschappen, maar het is duurder dan polyesterhars. Een belangrijk kenmerk van vinylester is dat het een uitstekende secundaire hechtsterkte heeft, zodat schotten of stringers toegevoegd aan een uitgeharde romp een betere hechting hebben dan op een polyester romp.
Epoxy:
Dit is hoogwaardige hars, met een passend prijskaartje. Epoxyharsen hebben een reputatie voor het zijn moeilijk om te werken sinds de vroege epoxies waren dik, maar veel moderne epoxies zijn vrij vloeibaar. Epoxy hecht beter dan elke andere hars aan een breed scala aan materialen, waardoor het ideaal is voor het bevestigen van kernen, stringers of andere items.
soorten Glasvezeldoek
weefsels die gebruik maken van continue strengen zijn de meest voorkomende doeken, met een gewicht variërend van 4 tot 15 ounces per vierkante meter. Zwaardere gewichten, meestal genoemd roving of geweven roving, bestaan uit niet-getwist garens van vezels in gewichten die variëren tot 48 ounces per yard. De afgewerkte roving lijkt op een grove jute en heeft, zoals alle doeken, een goede bi-directionele sterkte. De lichtere doekgewichten zijn te vinden in verschillende weefpatronen, zoals twill, satijn en mat, voor verschillende doeleinden.
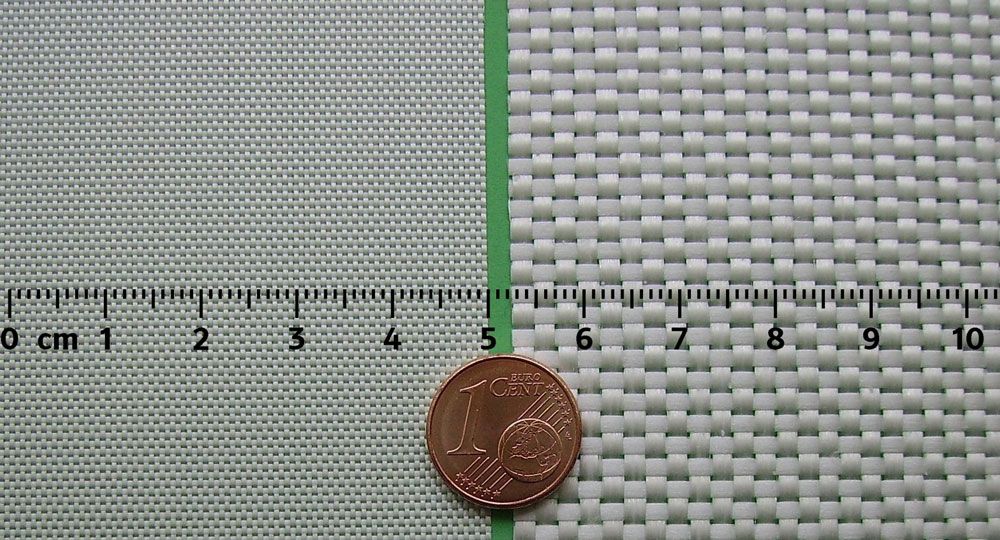
twee voorbeelden van glasvezel doek: de glasvezel aan de linkerkant is aanzienlijk dunner en lichter, maar biedt minder stijfheid.
E-glas:
Dit is het meest gebruikte glasvezel doek in de scheepsbouw vandaag. U kunt E-glass kopen bij een marine supply store, en verlijmen met polyesterhars. Het is gemaakt van gesmolten plastic gesponnen tot fijne vezels die vervolgens ofwel geweven in doek of losjes verzameld in zwerven.
s-glas:
Dit is hoogwaardig glasvezel doek uit de vliegtuigindustrie. Het is drie tot vijf keer duurder dan E-glass, maar het is ook veel sterker. Ontwikkeld door Owens-Corning, heeft het 20 tot 40 procent meer treksterkte, impact en buigsterkte dan E-glass. Er zijn twee soorten S-glas: S-1, die voldoet aan kritische lucht-en ruimtevaart normen en is verblindend duur; en S-2, die wordt gebruikt in de maritieme industrie. In Europa wordt S-glas R-glas genoemd.
Mat:
Mat is meestal gemaakt van E-glas en bestaat uit willekeurige vezels van twee tot drie inch die op hun plaats worden gehouden door een bindmiddel dat oplosbaar is in hars. Mat wordt voornamelijk gebruikt voor het bouwen van dikte en stijfheid in glasvezel lay-ups. Mat is bestand tegen” print-through”, waar het weefsel van roving te zien is in de buitenste laag van de romp, maar het absorbeert ook een enorme hoeveelheid hars en is laag in sterkte voor zijn gewicht.
Uni-directionele vezels:
Dit is een van de vooruitgang in het versterken van materialen. Het bestaat uit strengen vezels die slechts in één richting lopen, bij elkaar gehouden door enkele vezels die lateraal zijn gelijmd of genaaid, ongeveer op dezelfde manier dat een bamboe hek bij elkaar wordt gehouden door een paar draden. Uiteraard heeft het een zeer hoge richtingssterkte, zodat het kan worden gebruikt in gebieden waar de belastingen specifiek zijn. Omdat het niet geweven is, zijn er geen kniks en is het makkelijker voor werknemers om te nat worden met hars omdat het geen lucht vasthoudt als een stoffen stof.
Biaxiale vezels:
technisch gezien is de meeste stof biaxiaal, maar de moderne definitie betekent een stof gemaakt van lagen unidirectionele stof die niet door elkaar heen zijn geweven. Een laag ligt gewoon bovenop de volgende laag om een knikvrije band van vezels te produceren.
Tri-axiale vezels:
Dit is een gelaagd materiaal vergelijkbaar met bi-axiale doek, behalve dat de vezels zijn georiënteerd in drie richtingen, vaak op 120 graden naar elkaar om de belastingen te spreiden.
geavanceerde glasvezel Bouwmaterialen
koolstofvezel:
deze vezels van grafiet bieden een uitstekende stijfheid en hoge trek-en druksterkte en worden vaak gebruikt in combinatie met S-glas of andere exoten om een aanvaardbare slagvastheid te bieden, die anders vrij laag is. Koolstofvezel is erg duur, maar het kan beter presteren dan metaal in veel situaties. Veel bedrijven produceren wereldwijd koolstofvezel en het gebruik is afhankelijk van het koolstofgehalte van de vezel zelf, waarbij sommige bedoeld zijn voor toepassingen met hoge sterkte en andere gericht zijn op situaties met een hoge modulus (stijfheid). Het is de duurste vorm van vezelversterking beschikbaar, kost zo veel per pond als 100 keer gemeenschappelijke E-glas. Tweede alleen Kevlar in specifieke sterkte, koolstofvezels zijn superieur aan elke andere vezel in stijfheid.
Kevlar:
De handelsmerk naam voor een DuPont product, het wordt gebruikt om te verwijzen naar Aramide vezels waarvan Du Pont is de enige producent wereldwijd. Kevlar, een aromatische polymide (meestal afgekort tot aramide), is een vorm van nylon die oorspronkelijk werd ontwikkeld in het midden van de jaren 1960 als “Fiber B” om radiale bandbanden te versterken. De unieke eigenschappen werden al snel voor andere doeleinden gebruikt, en het publiek denkt meestal aan Kevlar in termen van kogelvrije jassen. Er zijn in feite twee vormen van Kevlar beschikbaar. Kevlar 29 wordt gebruikt voor lijnen, kabels en flak jackets, terwijl Kevlar 49 wordt gebruikt als versterkingsvezel in plastic composieten. Op een sterkte-gewicht vergelijking, Kevlar heeft de hoogste specifieke treksterkte van elke commerciële vezel. Het is vijf keer sterker dan staal en twee keer zo sterk als E-glass, waardoor een Kevlar romp dezelfde sterkte behoudt als een e-glass romp bij een fractie van het gewicht. Slagsterkte is ook een Kevlar forte, en het is in staat om herhaalde schokken te weerstaan en weerstand te bieden aan de neiging van andere versterkende vezels om scheuren te verspreiden. De negatieve kant van Kevlar is een duidelijke zwakte in compressiesterkte, dus het wordt vaak gebruikt in combinatie met andere vezels die die eigenschap balanceren.Nomex: een chemische stof ontwikkeld door DuPont, Nomex is het meest bekend om zijn brandwerende eigenschappen, en het wordt gebruikt in brandwerende pakken voor brandweerlieden en coureurs. Het is een aramide, die wordt omgezet in een papierachtige stof voor gebruik in honingraat.
hybriden:
Dit zijn versterkende weefsels die twee of meer verschillende soorten vezels combineren. Een veel voorkomende hybride is een mengsel van Kevlar met koolstofvezel. Het Kevlar zorgt voor een hoge slagvastheid, terwijl de koolstofvezel zorgt voor de stijfheid. Combinaties van S-glas, Kevlar en koolstofvezel zijn ook beschikbaar om bepaalde eigenschappen te optimaliseren tegen minimale kosten.
geavanceerde kernmaterialen
kernmaterialen worden vaak gebruikt om gewicht te verminderen en stijfheid te verhogen. Sommige bouwers core de hele boot; anderen bouwen met massief glasvezel van de waterlijn naar beneden en ontkernen boven, en weer anderen gebruiken een mix van ontkernen en massief glas in de hele boot.
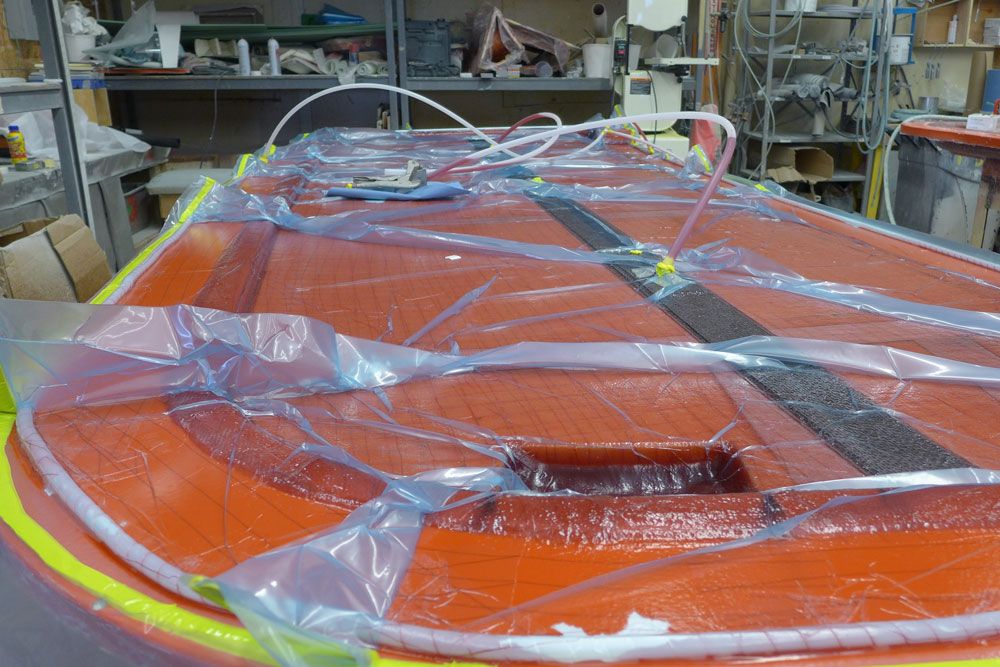
u kunt de kern (met geruit uiterlijk) in dit deel zien, die op het punt staat vacuüm te worden verpakt bij Sabre Yachts. Foto Door: Sabre Yachts.
Balsakern:
bij het eerste gebruik als een rompversterker legden bootbouwers lange planken balsa in de rompen, maar deze methode leidde tot rotting en structurele storing wanneer water “slecht” door de hele plank. Het heeft lang geduurd voordat balsa in dit begin leefde, maar moderne balsa is nu een algemeen aanvaard boormateriaal in Boten. De oplossing kwam van het snijden door de korrel, draaien op de rand, en het produceren van een dambord patroon van eindkorrel stukken die geen water overbrengen. Het resultaat is een stijve, lichte en goedkope kern met een goede impactkwaliteit en een hoge druksterkte. Een extra eigenschap is de isolatiekwaliteit van balsa tegen geluid, thermische verandering en trillingen. Een negatieve factor is dat balsa hars kan absorberen, waardoor de romp zwaarder, maar kwaliteit vakmanschap kan voorkomen dat dat gebeurt.
PVC-schuim:
Airex en Klegecell (spreek uit: kladge-a-cell) zijn de populairste commercieel geproduceerde schuimkernen die tegenwoordig worden gebruikt. Beide zijn gesloten celschuimen gemaakt van polyvinylchloride, maar elk heeft verschillende kenmerken. Airex is een niet-Vernet PVC, waardoor het flexibeler en bestand tegen schade. Klegecell is een Vernet schuim dat extreem stijf is. In het buitenland gebouwde boten maken vaak gebruik van Divinycell, een Scandinavische versie van Klegecell.honingraat:
honingraat is precies wat het klinkt: een wafelachtig patroon van materiaal dat de hoogste stijfheid geeft van elke kern van gelijk gewicht. De compressie en afschuifsterktes zijn ongeëvenaard, wat kan worden verwacht van een materiaal dat oorspronkelijk werd gebruikt in vliegtuigen voor vloeren en schotten. Nomex honeycomb is de meest voorkomende op jachten, hoewel het is zeker een high-ticket extravagantie voor eigenaren op zoek naar de laatste ounce van gewichtsbesparing. Verrassend genoeg zijn sommige honingraten van papier gemaakt. Een kraftpapier wordt geïmpregneerd met harsen en vervolgens gevormd tot een honingraat, waardoor het waterbestendig en stevig is, maar het papier honingraat is zwaarder dan Nomex. “Gevilde panelen” zijn kant-en-klare platen van honingraat die lijken op een stuk triplex, en zijn verkrijgbaar met teak fineer of diverse andere overlays die kunnen worden gesneden in kant-en-klare honingraatschotten.krijg wat inzicht in hoe core werkt in een glasvezel deel door te kijken naar onze Understanding Foam Cored Boat Construction video.
geavanceerde technieken voor het bouwen van boten
samen met deze nieuwe materialen zijn de methoden om ze op te leggen in wat uiteindelijk een boot zal worden ook de laatste jaren vooruitgegaan. Nogmaals, het minimaliseren van gewicht terwijl het maximaliseren van kracht is vrijwel altijd het doel.
vacuümzakken
: Dit proces begint als een open vormopstelling, maar het natte laminaat is ingesloten in een plastic folie en er wordt een vacuüm aangebracht om overtollig hars te onttrekken. Overtollige hars voegt geen kracht toe – daar is de glasvezel voor-maar het voegt wel gewicht toe. Dus het vacuümzakproces vermindert het uiteindelijke gewicht van de boot zonder enige kracht op te offeren.
vacuüminfusie
: Het vacuüminfusieproces omvat eveneens kunststoffolie en een vacuüm om een ideale hars / glasverhouding te bereiken. Echter, in plaats van te beginnen met een natte lay-up het vacuüm, samen met een set van hars voeden lijnen, introduceert en trekt de hars door het doek in de eerste plaats. Dit zorgt voor een nauwkeuriger meting van de materialen en de mogelijkheid om een gelijkmatige druk toe te passen op een groot gebied, zodat u grotere delen kunt leggen.
voor een vereenvoudigde uitleg van hoe het vacuümproces werkt bij het vormen van boten, kijk dan naar onze Understanding Vacuum Bagging video.
alternatieve methoden voor het bouwen van boten
hoewel de overgrote meerderheid van de pleziervaartuigen die vandaag worden gebouwd, afhankelijk zijn van deze materialen en methoden, zijn er uitzonderingen. Meestal vind je ze bij grote jachten, waar de prijs geen probleem is. Sommige zijn nog steeds gebouwd met metalen rompen, en sommige anderen met technieken zoals ” koude molding, “of” plank op frame.”In deze gevallen is de structuur van de boot gemaakt van hout dat vervolgens wordt gelaagd met of ingekapseld in met de hand gelegde glasvezel en epoxyhars. Sportvissen jachten zoals een Bayliss 73 voet cabriolet, en high-end cruisers zoals Vicem jachten, zijn gebouwd met deze methoden.
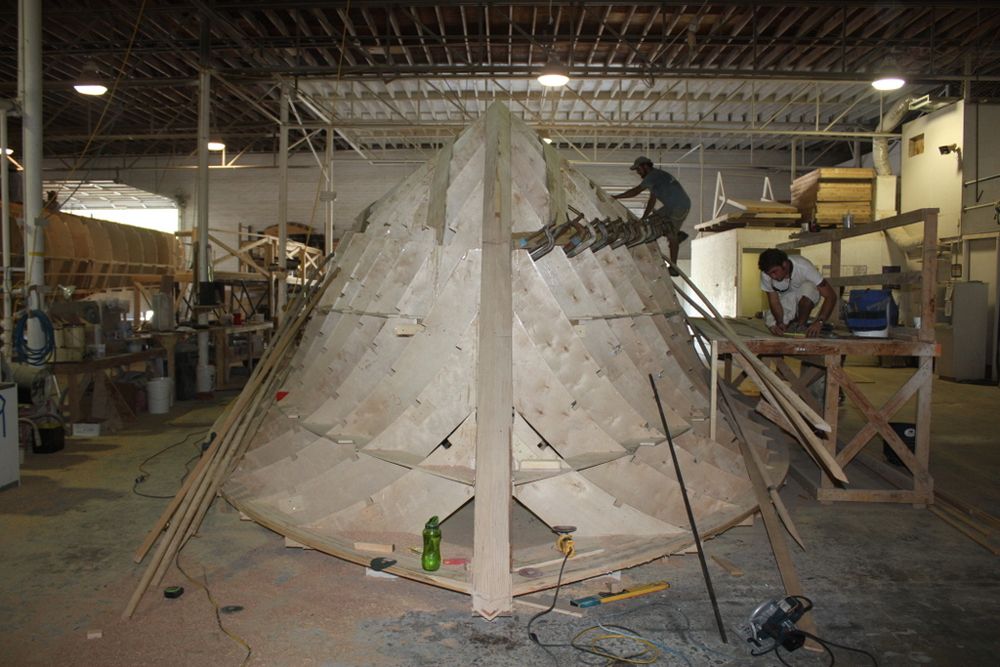
hoewel veel moderne boatbuilders het gebruik van hout vermijden, worden op high-end custom yachts zoals deze Jarrett Bay, methoden zoals koudgieten vaak beschouwd als superieur aan meer moderne technieken.
aan de andere kant van het uiterste, heb je FRP boten zonder de F of de R en alleen de P – plastic. Hoewel de grootste alle-plastic boten in productie zijn minder dan 20 voet in lengte (en de meeste zijn minder dan 12 of 14 voet) roto-gegoten plastic is heel populair geworden in de kajak en dinghy markten. Deze eenvoudige, goedkope ambachtelijke worden gevormd uit plastic pellets die worden gesmolten in een roterende oven, die ook een mal. Als het afkoelt, heeft het plastic de vorm van de mal aangenomen en springt er een boot uit.
nu u de basisprincipes van het moderne bouwen van boten kent en u klaar bent om een eigen boot te kiezen, lees dan zeker hoe u een boot koopt: Tips voor eerste kopers.Noot van de redactie: Dit artikel bevat delen van een basis-Bootbouwartikel van Chris Caswell, uit augustus 2000, en is bijgewerkt in oktober 2018 en maart 2020.